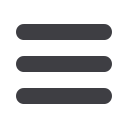
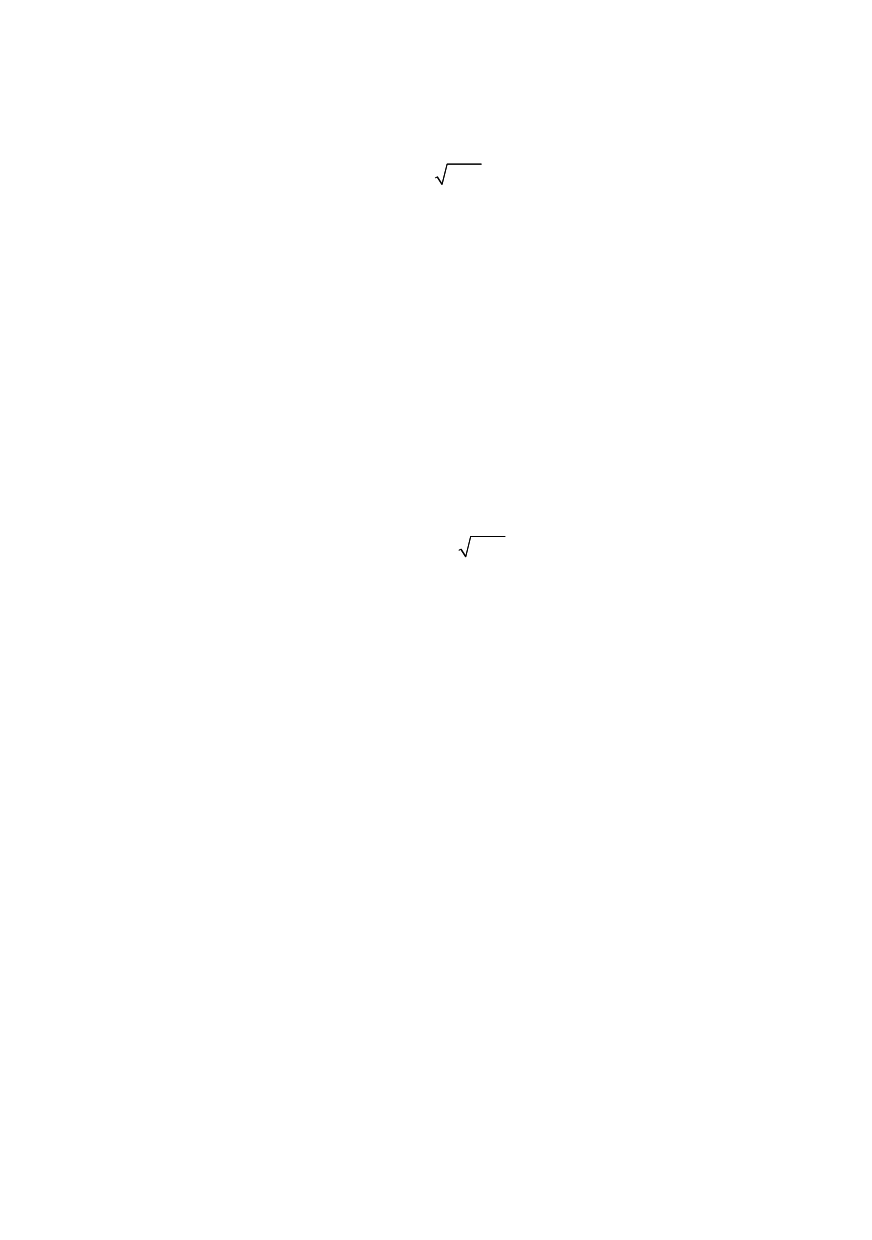
94
This formula allows an appreciation of the combined influence of stress and crack
length. Stress intensity depends directly, but not singularly, on stress, and it depends on
crack length. In a more general format, stress intensities might be expressed as:
I
K
a Y
σ
π
= ⋅
⋅ ⋅
(2)
where
Y
is a geometric factor allowing the representation of other geometries.
In fact, a stress can never be applied, but a load can. Stress is a resultant and determi-
ned quantity; it is not measurable. It is a mathematical tool of useful characteristics and
provides interpretations and insights, especially in reflecting an areal rationalized force
(load) path through the structure. Structures and materials, however, only experience
loads (mechanical, thermal, chemical) and respond with displacements and strains.
In some cases, however, where complexity precludes a simple "stress" approach,
analytical techniques do allow the calculation of stress intensity factors under the
imposed loads. The connection of stress intensity,
K
I
, as a controlling quantity for fracture
is a direct consequence of a physical model for LEFM under plane-strain conditions. Its
limit is
K
Ic
, the critical plane-strain fracture toughness. The use of the stress intensity
range, Δ
K
I
, as a controlling quantity for crack extension under cyclic loading is simply by
correlation. The ability of the stress intensity to reflect crack-tip conditions remains
mathematically correct, but the correlation of Δ
K
I
to crack growth is successfully
demonstrated. By altering Eq. (1) using
Δσ
instead of
σ
, Δ
K
I
results in:
I
K
a
σ
π
Δ = Δ ⋅
⋅
(3)
The stress intensity factor range to a certain extent simply reflects an extension of the
stress-based practices. However, the testing to support fracture mechanics-based fatigue
data is done differently than in the
S
-
N
or -
N
methods because of the necessity to monitor
crack growth. Crack growth testing is performed on samples with established
K
I
vs.
a
relation. Under the controlled load specified using two dynamic variables, the crack
length is measured at successive intervals to determine the extension over the last incre-
ment of cycles. Crack length measurement can be done visually or by mechanical or
electronic devices using established techniques that allow for automation of the process.
The result from the testing is not crack growth rate,
da
/
dN
, but
a
versus
N
. Next nume-
rical differentiation of the
a
-
N
data set using provides
da
/
dN
versus
a
. Coupling this latter
data with a stress intensity factor expression (
K
I
as a function of load and crack length)
for the specific sample results in the final desired plot of
da
/
dN
versus
ΔK
I
. This process
is shown schematically in Fig. 7. The
da
/
dN
versus
ΔK
I
curve has a sigmoidal shape, and
a full data set covers crack growth rates that range from fatigue crack threshold to frac-
ture. It is to note that this data represents only "long crack" behaviour; that is, the cracks
are substantially greater in size than any controlling microstructural unit (e.g. grain size)
and typically exceed several millimeters in length. A second important assumption is that
of a plane-strain stress state; therefore, a plane-stress descriptor is not required.
A real test of modelled
da
/
dN
vs.
ΔK
I
expressions is whether, under reintegration, the
original
a
-
N
data will be reproduced. The generation of
da
/
dN
vs.
ΔK
I
data is obviously
more involved than either
S
-
N
or ε-
N
testing. It does have the advantage, however, of
producing multiple data points from a given test. Figure 8 reflects interesting features at
each extreme of the
da
/
dN
vs.
ΔK
I
curve. First, at the upper limit of
ΔK
I
, it reaches the
point of instability and the crack growth rate become very large as fracture is approached.