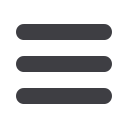
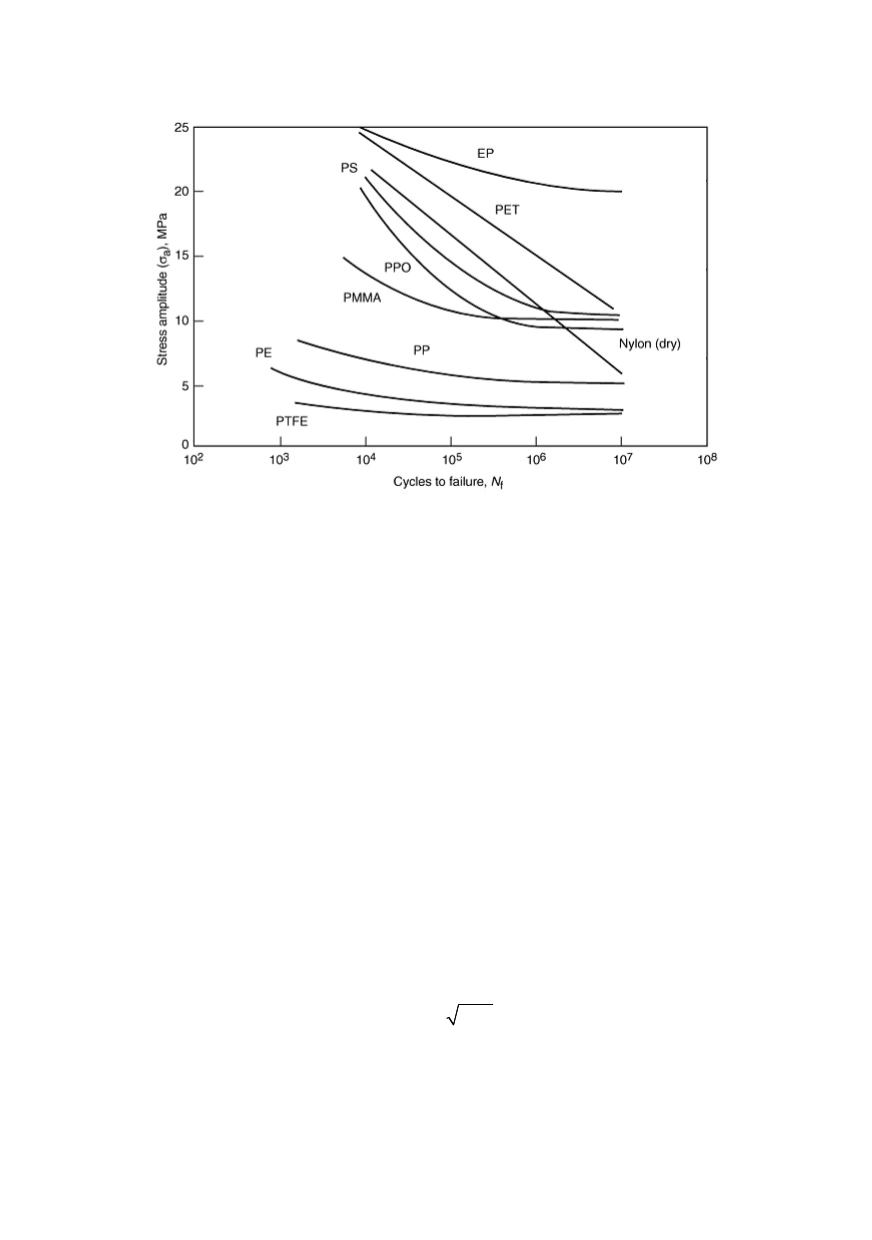
93
Figure 6: Typical fatigue-strength curves for different polymers (30 Hz test frequency) /14/
In multiaxial stress states the difficulty occur in identifying an appropriate "stress",
and the stress-life technique offers then a variety of advantages. Its extension using strain
as a controlling quantity is a natural progression of technology.
4. DAMAGE TOLERANT CRITERION: FRACTURE MECHANICS IN FATIGUE
The
S
-
N
and ε-
N
techniques are usually appropriate when a component or structure
can be considered a continuum (i.e. “no cracks” assumed). they can’t be applied when a
crack-like discontinuity is present. The fact that components with "cracks" may continue
to bear load is generally not acceptable using either
S
-
N
or ε-
N
methods.
One reason is the inability of the controlling quantities to allow the presence of a
crack. A brief review of basic elasticity calculations shows that both stress and strain
become infinite at a crack due to elastic stress concentration. Even induced plasticity still
leaves low tolerable loads. An alternative concept and controlling quantity is required.
That quantity is
stress intensity,
a characterization and quantification of the stress field
near the crack tip, base of linear elastic fracture mechanics (LEFM). It recognizes the
singularity of stress at the tip and provides measurable material property.
The development of fracture mechanics has roots in the early 1920s and mainly has
developed since the late 1940s and early 1950s. A very basic expression for the stress
intensity is its determination for a semi-infinite center-cracked panel having a through-
thickness crack of length 2
a
in a uniform stress field
σ
that is operating normal to the
opening faces of the crack. The resulting stress intensity factor
K
I
is as follows /15/:
I
K
a
σ
π
= ⋅
⋅
(1)
where is the far field stress responsible for opening mode loading (mode I) and
a
is the
crack depth in from the edge of the plate.