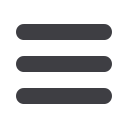
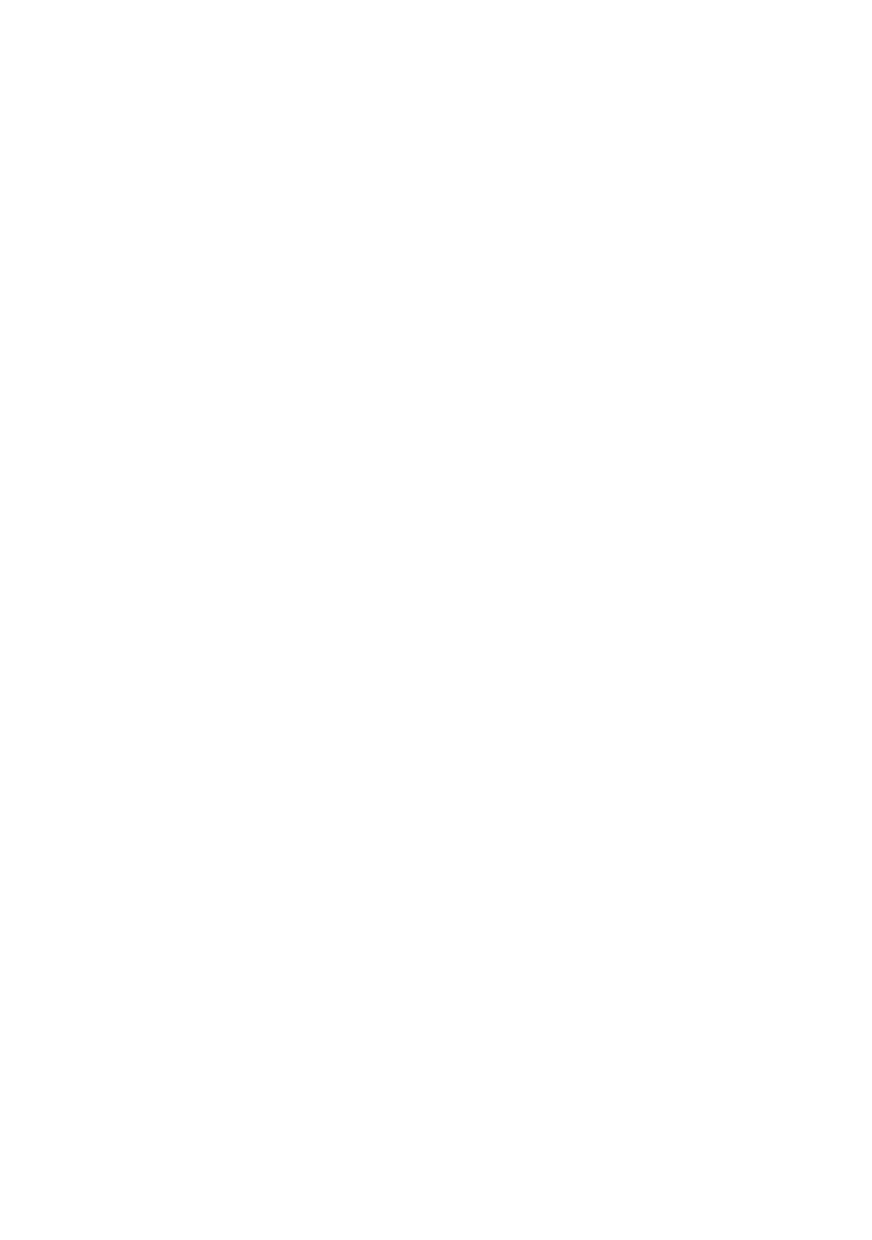
89
to bear load and can operate safely for extended periods of time. Developments from the
1960s and before have produced the third design philosophy, damage tolerant. It is
intended expressly to address the issue of "cracked" components.
When a crack is present, an alternative controlling quantity is involved, as mode I
stress intensity factor range, (Δ
K
I
), a function of crack location, orientation, and size
within the geometry of the part. This fracture mechanics parameter is then related to the
potential for crack extension under the imposed cyclic loads for subcritical growth or the
initiation of unstable fracture. It is quite different from the other two approaches. Property
descriptions for the crack extension under cyclic loading are typically
da
/
dN
- Δ
K
I
curves
(log crack growth rate vs. log stress-intensity range), Table 1.
The advantage of the damage tolerant design philosophy is the ability to treat cracked
objects in an appropriate fashion. The previous methods only allow for the immediate
removal of cracked structure, and here the number of cycles of crack growth over a range
of crack sizes can be estimated and fracture to be predicted. The clear tie of crack size,
orientation, and geometry to non-destructive testing (NDT) is also a benefit. Disadvan-
tages are connected with complexity in development and modelling of property data, and
required numerical integration for crack growth. The predicted lives are influenced by the
initial crack size, requiring quantitative determination of detection probability for each
type of NDT method used.
3. INFINITE-LIFE CRITERION (
S
-
N
CURVE)
Safe-life design based on the infinite-life criterion reflects the classic approach to
fatigue. It was developed through the 1800s and early 1900s because complex machinery
of that time increasingly produced dynamic loads, followed by increasing number of
failures. The safe-life, infinite-life design philosophy was the first to address this need.
The stress-life or
S
-
N
approach is one of a safe-life, infinite-life regime. It is categori-
zed as a "high cycle fatigue", with most considerations based on maintaining elastic
behaviour in the examined object. The "no cracks" is accepted, although all test results
inherently include the influence of the discontinuity population present in the object.
In this period steel was dominant metallic structural material (land transportation,
power generation, constructions). The "infinite-life" aspect of this approach is related to
the asymptotic behaviour of steels, many of which exhibited a fatigue limit or "enduran-
ce" limit at a high number of cycles (>10
6
). Most other materials do not exhibit this
response, displaying a continuously decreasing stress-life response, even at a great num-
ber of cycles (10
6
to 10
9
), more correctly described by fatigue strength at a given number
of cycles. Figure 1 shows a schematic comparison of these two characteristic results.
Many machine design texts cover this method to varying degrees /4-8/.
What about the
S
-
N
data presentation? Stress is the controlling quantity in this method.
The most typical formats for the data are to plot the log number of cycles to failure
(sample separation) versus either stress amplitude (
S
a
), maximum stress (
S
max
), or stress
range (Δ
S
) /9, 10/. Figure 2 provide plots for three constant-
R
value tests (
R
is the ration
of minimum and maximum stress in a cycle, the second dynamic variable). Note the
apparent reversal of the effect of
R
, although the data are identical. Clearly, while the
analytical result must be identical regardless of which graphic means is employed, the
visual influence in interpretation varies with the method of presentation.
Mean stress influence is important, and design approach must consider it. According
to Bannantine et al. /7/, the archetypal mean stress (S
m
) versus stress amplitude (
S
a
)