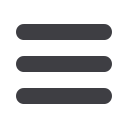
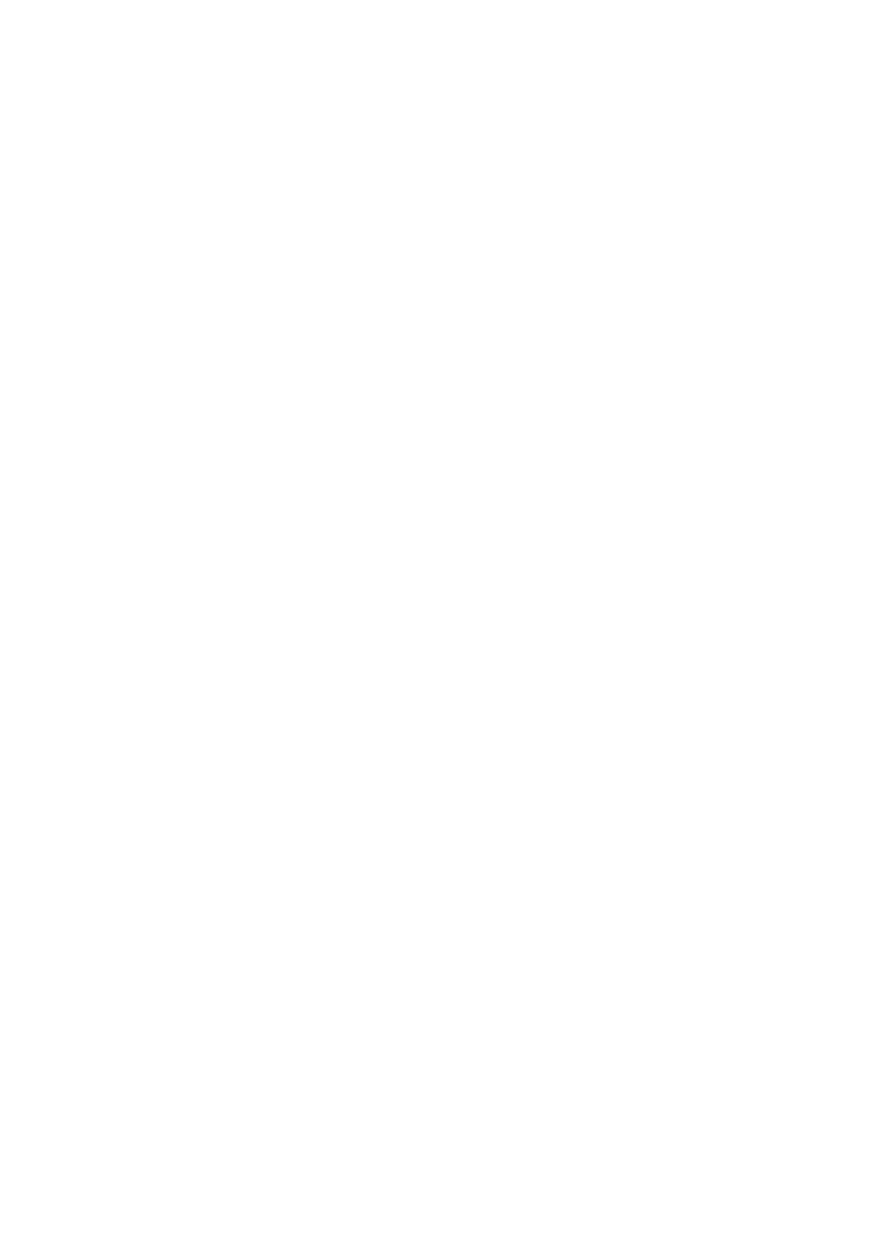
97
It has been shown that specimen thickness has no significant effect on the FCGR
behaviour /20/, although that is not always the case. The ability of
ΔK
to account for so
many variables has tremendous significance in the application of the data. Thus, the
FCGR behaviour expressed as
da
/
dN
versus
ΔK
can be regarded as a fundamental mate-
rial property analogous to the yield and ultimate tensile strength, or plane strain fracture
toughness,
K
Ic
, /21/. Knowing this property, prediction of the crack length vs. cycles
behaviour of any component using that material and containing a preexisting crack or
crack-like defect can be obtained, as long as the fatigue stresses in the component are
known and a
K
expression for the crack/load configuration is available.
This is a simple exponential relation that can readily be curve fit to the desired data
portion, Fig. 9. Stress or load ratio affects crack propagation data as well. The influence is
that increasing
R
(here
R
=
K
min
/
K
max
) decreases both the threshold value at the low end
and the instability at the up end of the da/
dN
vs.
ΔK
curve ( Fig. 10 /22/, Fig. 11 /8/).
Like other mechanical properties, microstructure affects also fatigue crack growth
characteristics. An example, given in Fig. 12, shows the combined influence of both
gamma prime and grain sizes on fatigue crack propagation in Waspaloy.
Plastics also can be analysed using this technique. Figure 13 shows a variety of
materials that are displayed in the conventional form. Many polymeric materials exhibit
substantial frequency effects, and this should be considered in the generation of data.
In application, use of
da
/
dN
versus Δ
K
I
is completely different than either the
S
-
N
or
ε-
N
continuum method. Instead of providing an immediate life estimate in association
with a given stress or strain combination and a test coupon's modelled failure criterion, a
more complicated determination is required. Using the
a
versus Δ
K
I
relation in the part,
the applied loads are employed to assess crack extension over incremental changes in
length, and they are continuously summed to reflect the total increase. In essence, this is
the regeneration of the
a
-
N
curve for the specific part. Crack growth can be assessed until
fracture (achieving a critical crack size) or some other intermediate point.
It is common in several industries to use the above technique to determine intervals
between inspections to ensure structural integrity. So formulated inspection schedules
maximises the probability to detect discontinuity only in an extended, critical stage, enab-
ling to use advantages of the damage tolerant approach. Even on this technique, a crack,
once discovered, can’t necessarily be left. Removal or structural modification may be the
only acceptable alternative (e.g. in airframes). The predictive aspects of the technique can
justify continued operation under full or derated conditions till requested replacement
parts or with a stated finite-life limit for the unit (extra inspections may be required). By
probabilistic methods a quantified risk assessment can be assessed.
4.2. Test procedure
American Society for Testing and Materials (ASTM) Standard E647 /25/ is the accep-
ted guideline for fatigue crack growth rate (FCGR) testing and is applicable to a wide
variety of materials and growth rates. The testing consists of several steps, starting with
selecting the specimen size, geometry, and crack length measurement technique. When
planning the tests, the investigator must respect of the application of FCGR data. Testing
is often performed in laboratory air at room temperature; however, any gaseous or liquid
environment and temperature may be used to determine the effect of temperature and cor-
rosion on cyclic loading. Cyclic loading also may involve various waveforms for cons-
tant-amplitude loading, spectrum loading, or random loading.