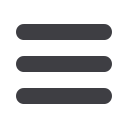
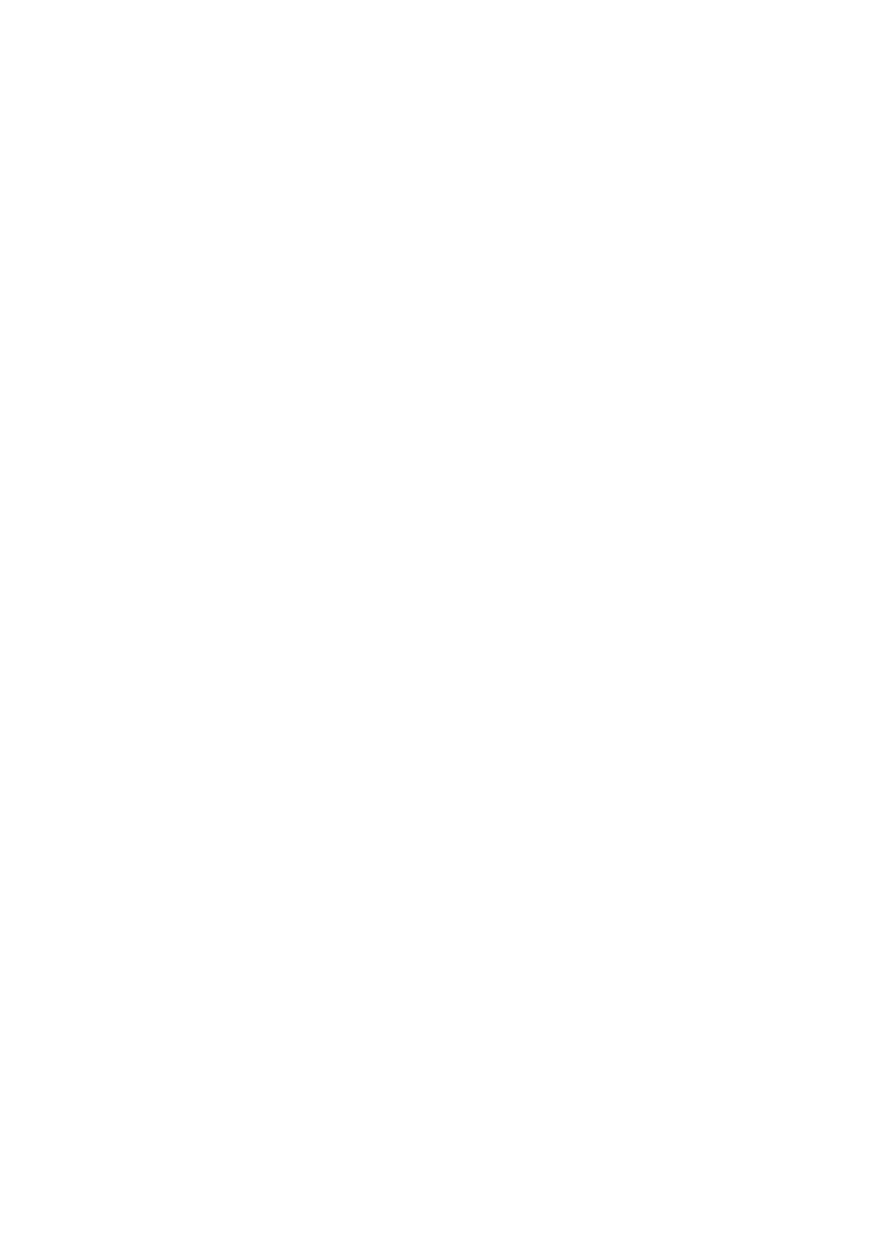
99
In the threshold and the low-growth regime FCGR testing (region I in Fig. 8)
acquisition of valid and consistent data is complicated, since the crack growth behaviour
is more sensitive to the material, environment, and testing procedures. Within this regime,
the material fatigue mechanisms that slow the crack growth rates are more significant.
It is expensive to obtain a true value of
ΔK
th
. In some materials it does none exist.
Designers are more interested in the fatigue crack growth rate at threshold regime, e.g.
ΔK
corresponding to a fatigue crack growth rate 10
-8
to 10
-10
m/cycle. Because the
duration of the tests increases for each decade of near-threshold data (10
-8
to 10
-9
to 10
-10
),
the precise requirements should be determined before the test. ASTM Standard E- 647
addresses these requirements, but the methods for fatigue crack threshold test may differ.
In all areas of crack growth rate testing, the resolution capability of the crack measu-
ring technique should be known, what is more important in the threshold regime. The
smallest amount of crack length resolution as possible is desired, because the rate of
decreasing applied loads (load shedding) is dependent on how easily the crack length can
be measured. The minimum amount of change in crack growth that is measured should be
ten times the crack length measurement precision. It is also recommended that for non-
continuous load shedding testing, where [(
P
max
-
P
min
)/
P
a
] > 0.02, where mean value is
accepted as
P
a
= (
P
min
+
P
max
/2), the reduction in the maximum load should not exceed
10% of the previous maximum load, and the minimum crack extension between load
sheds should be at least 0.50 mm.
4.2.1. Specimen type selection
In selecting a specimen, the resolution capability of the crack measuring device and
the
K
-gradient (the rate at which
K
is increased or decreased) in the specimen should be
known. If the measuring device is not suitable, the threshold crack growth rate may not
be achieved before the specimen is fractured. When a new crack-length measuring device
is applied, a new type of material used, or some factor is different from previous testing,
the
K
-decreasing portion of the test should be followed with constant load amplitude (
K
-
increasing) to make the methods comparable. With consistency achieved, constant-load
amplitude testing at the low crack growth rate is not necessary in similar conditions.
Three types of specimens used in FCGR testing are commonly used: pin-loaded (Figs.
14, 15), bend-loaded (Fig. 16.a) and wedge-gripped specimens (Fig. 16.b, c, d). Precisely
machined specimens are essential, and ASTM E 647 specifies the tolerances and
K
-
calibrations for compact-type C(T) and middle-tension M(T) geometries. Single-edge
bends SE(B), arc-shaped A(T), and disk-shaped compact DC(T) specimen geometries and
their
K
-calibrations are discussed in ASTM E 399. Similar tolerances should be specified
for "nonstandard" specimens. The selection of an appropriate geometry depends on
material availability and row form, desired loading condition, and equipment limitations.
The most widely used types of specimens are M(T) (Fig. 14), and C(T) specimens
(Fig. 15). However, any specimen configuration with a known stress-intensity factor
solution can be used in fatigue crack growth rate testing, assuming that the appropriate
equipment is available for controlling the test and measuring the crack dimensions.
4.2.2. Specimen size, crack length and microstructure consideration
The applicable range of the stress-intensity solution of a specimen configuration is
very important. Many stress-intensity expressions are valid only over a range of the ratio
of crack length to specimen width (
a
/
W
). The expression given in Fig. 14 for C(T)