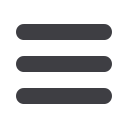
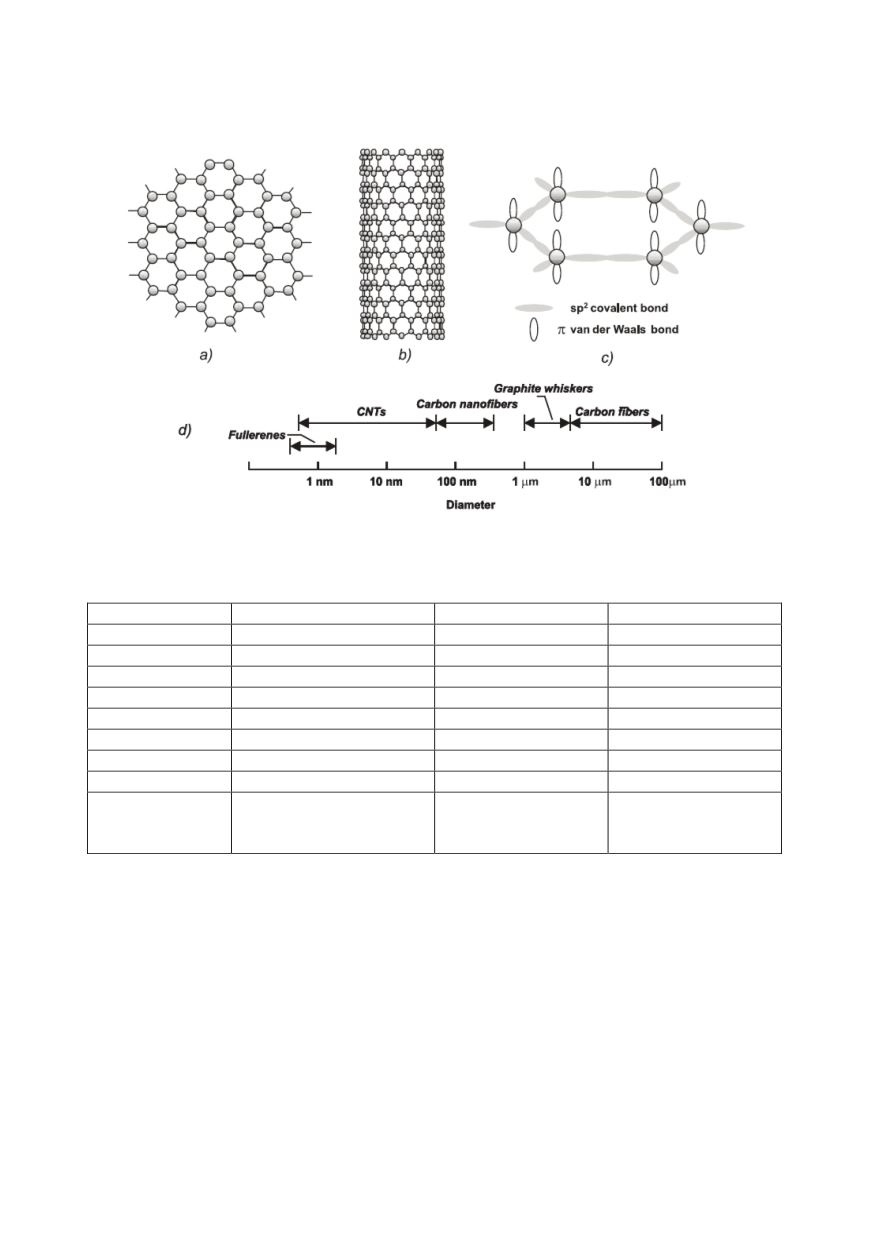
336
found for structural components. In practice this is not sufficient for reliable service of
structures and energy parameters should be used in addition, such as toughness.
Figure 15: a. Monolayer of carbon atoms. b. Single-walled nanotube (SWNT). c. Covalent bond
between basal carbon atoms and bond between basal planes. d. diameters of carbon materials
Table 2: Modulus of elasticity, fracture stress and strain for structural materials (based on /1/)
Material
Modulus of elasticity, TPa Fracture stress, GPa
Fracture strain, %
Steel 4340
0.207
1.6 ÷ 1.7
12
Tungsten
0.4
0.76
3.5
Zirkonia (ZrO
2
)
0.2
0.8 ÷ 1.5
-
Kevlar fibres
0.06 ÷ 0.15
3.6 ÷ 4.1
2.5 ÷ 1
Epoxy
0.0035
0.005
-
Diamond
0.7 ÷ 1.2
1.05
-
Carbon fibres
0.20 ÷ 0.75
4.0 ÷ 7.0
0.5 ÷ 1.8
Carbon nano tube
1 (0.50 ÷ 5.50)
15 ÷ 63
5 ÷ 15
Carbon multiwall
nano tube
0.1 ÷ 1.2 (tension)
1.7 ÷ 2.4 (compression)
1.28 ± 0.59 (bending)
10 ÷ 66
100 ÷ 150
14.2 ± 0.8
-
-
-
Many assumptions and simplifications are induced for macro structures in order to
achieve uniform interpretation of parameter values. Following facts should be respected:
Stress is defined as the relation between of applied load and cross section properties
of component or specimen, neglecting the microstructure of material.
1.
Stress and strain tensors, applied in mathematical structural analysis, are defined for a
homogeneous continuum, and applied for inhomogeneous structure.
2.
Yield strength of material, determined by standardized testing method, again with
corresponding limitations, is generally accepted strength parameter in design.
Considering the dimension and composition of nano material it can be clear why the
strength parameters data of nano materials are not yet completely available, especially
those for CNT materials. In this case strength is also presented by the load in a moment