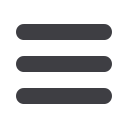
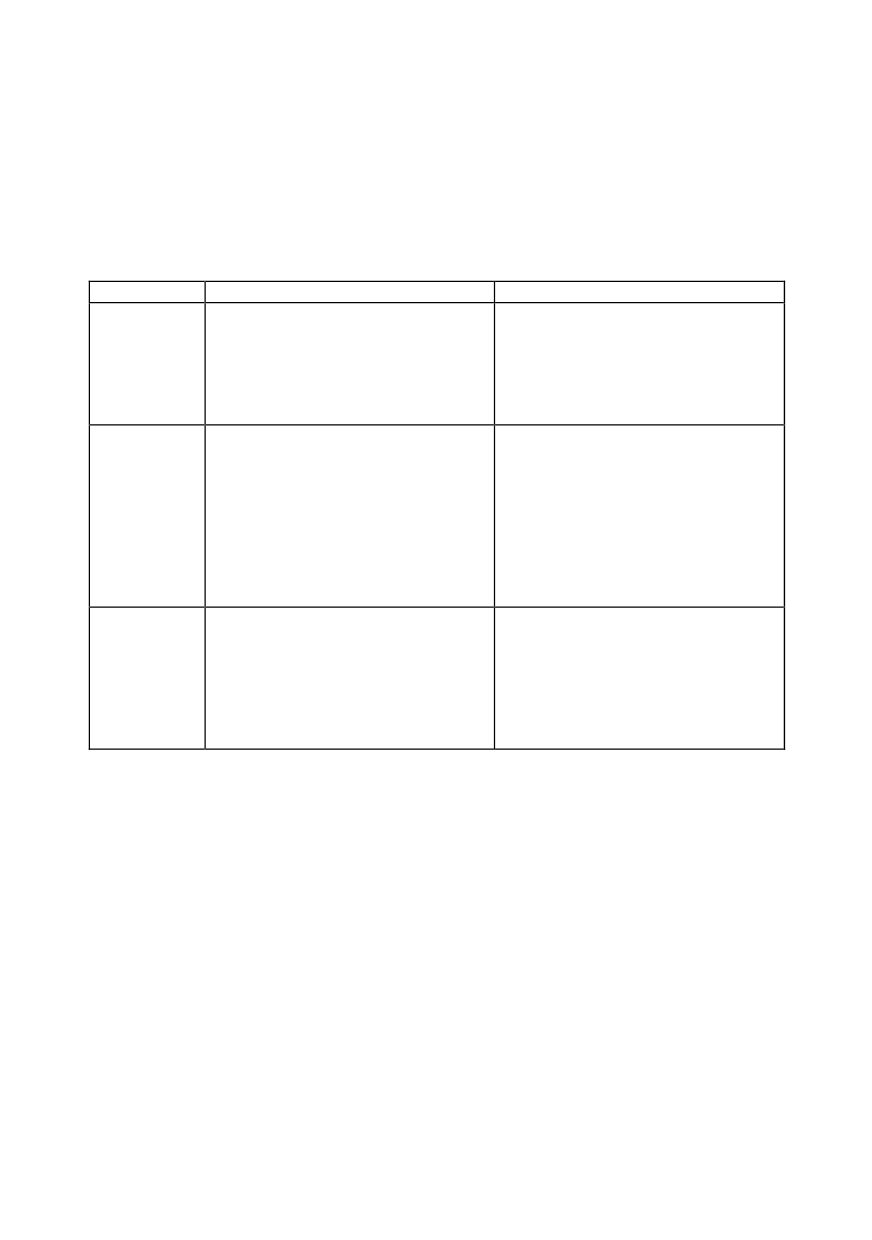
153
toughness values for the same material are higher than those obtained as
K
Ic
or
J
Ic
values.
Advantages and disadvantages of fracture toughness tests are listed in Table 2 /8-14/.
The three-point bend and compact specimens (standardized in ASTM E 399 and E
813) are recommended for general laboratory materials evaluation, because
K
and
J
cali-
brations for these specimens are known and relatively low loads are required during
testing. Data obtained with non-standard specimens must be evaluated carefully to ensure
that the same fracture criteria are used, such as the onset of cracking.
Table 2: Fracture toughness tests
Method
Advantages
Disadvantages
K
Ic
,
ASTM E 399
This method is the most reliable to get
fracture toughness values at lower
temperatures. The success of all other
methods is based on their ability to give
data comparable to this method.
The high cost of testing the large
specimens at high temperature tends to
reduce the number of data points. Linear
extrapolation from valid
K
Ic
at lower to
higher temperature is conservative. No
valid
K
Ic
values at high temperature.
J
-integral,
ASTM E 813
Provides fracture toughness values that
agree with
K
Ic
value. Fracture toughness
data at high temperature are realistic.
Sound theoretical basis permits evaluation
of stable crack growth. The value
dJ/da
is
a measure of the resistance to continued
crack propagation. Testing a series of
small
J
specimens provides an indication
of material toughness variation.
It is not possible to evaluate irregular
crack propagation due to residual stress or
at HAZ near welds. Not accurate enough
at low temperatures. Measurements are
inaccurate due to irregular crack fronts.
Not valid for thin materials where K
J
is
2.5
K
Ic
. When heat tinting is used, the
additional number of specimens increase
testing costs.
CTOD,
BS 7448
Provides fracture toughness values that
agree with
K
Ic
method. Fracture toughness
data at high temperature are realistic.
CTOD results are consistent and
comparable with the values of other
methods. Simultaneous measurement of
CTOD and
J
integral is possible.
Variations in the measurement of CTOD
(
δ
)
results in variations of
K
Ic
up to a
factor of 2. This method is restricted to
temperatures above -60°C.
A proper use of fracture-mechanics methodology for fracture control of structures
necessitates the determination of fracture toughness for the material at the temperature
and loading rate representative of the intended application. The morphology of fracture
surfaces for steel can be understood by considering the fracture-toughness transition
behaviour under static and impact loading, depicting the mode of crack initiation at the
crack tip for static, and the mode of crack propagation for dynamic loading.
This is to emphasize that one of the key problems regarding accuracy of fracture
mechanic testing of welded joints specimens is notch positioning, Fig. 8 /15/.
Experimental work experienced in methodological approach can help, as an example,
to understand better fracture mechanics parameters for BM, HAZ and WM, determined as
static and impact crack properties of high strength steel welded joint were tested /16 - 20/.
6. EXPERIMENTAL INVESTIGATION
Experimental investigations of the static and impact properties have been performed
with high strength (HSLA) steel NIONIKRAL 70 (NN70) of nominal yield strength 700
MPa, designed for pressure equipment in process industry and in shipbuilding, e.g. for
submarines. This is a quenched and tempered (Q&T), low alloy, Ni-Cr-Mo steel (Table