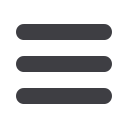
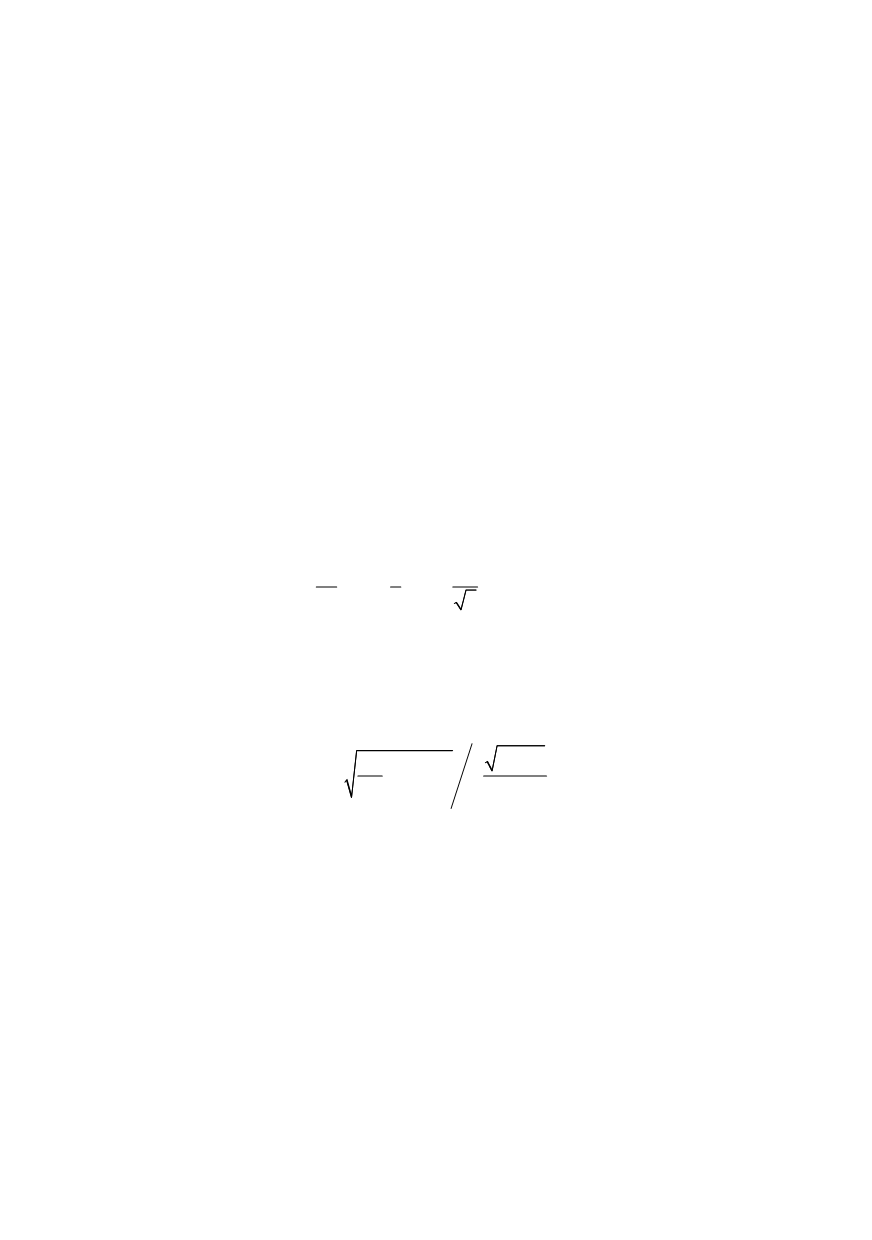
74
describe the process of ductile fracture in most metallic materials, the aim is to derive an
approach capable of taking into account the specific properties of the examined material.
3.2 Complete Gurson model (CGM)
As already explained, the GTN model describes the material as a continuum weakened
by the presence of voids. Such representation corresponds to so-called homogeneous
deformation mode. Damage function (9) can be used to model the loss of load-carrying
capacity of the material, but it cannot be directly linked with the actual processes during
the last stage of ductile fracture. Thomason /28/ proposed a more realistic failure
criterion, which is based on the analysis of deformation in the intervoid ligaments -
localised deformation mode. Localized deformation state of void coalescence differs from
the homogenous deformation state during void nucleation and growth. For small values of
external load, homogeneous state is dominant, because the intervoid ligaments are large.
With further increase of load, plastic strain grows, and these ligaments become thinner.
Therefore, the stress needed for localised deformation decreases. When this stress is equal
to the stress needed for the homogeneous deformation, the void coalescence starts.
Zhang et al. /21/ made a significant modification of the GTN model - they applied the
Thomason’s void coalescence criterion based on the plastic limit load model (with the
assumption that all the voids remain spherical during the increase of the external loading),
thus introducing the complete Gurson model - CGM. Criterion for determining the instant
when void coalescence starts is:
(
)
2
1
1 1
1
r
r
r
σ
β
α
π
σ
⎛
⎞
⎛
⎞
>
− +
−
⎜
⎟
⎜
⎟
⎝
⎠
⎝
⎠
(17)
Here,
σ
1
is the maximum principal stress,
α
= 0.1 and
β
= 1.2 are constants introduced by
Thomason /28/. Zhang et al. /21/ proposed a linear dependence of
α
on hardening
exponent
n
for elastic-plastic materials that exhibit strain hardening.
In Eq. (17),
r
represents the void space ratio /21/, i.e. the ratio of the void radius and
the intervoid distance:
2 3
1 2 3
3
3
4
2
f
e
r
e
ε
ε
ε
ε
ε
π
+
+ +
⎛
⎞
⎜
⎟
=
⎜
⎟
⎝
⎠
(18)
where
ε
1
,
ε
2
and
ε
3
are principal strains. Therefore, the critical void volume fraction
f
c
is
not a material constant in CGM - but the material response at void coalescence. The value
of
f
c
depends on the strain field, so it is not necessary the same in all finite elements and
in all integration points within one element. According to the CGM, ductile fracture initi-
ation is fully determined by Eqs. (8) and (9), with the criterion for void coalescence (17).
Micromechanical models for ductile fracture prediction described in Chapters 2 and 3
are continuously being improved through many on-going investigations, national and
international research projects. One of the aims is application of local approach to ductile
and cleavage fracture in structural integrity assessment, as shown in /29/.
4. CRACK GROWTH MODELLING
Besides the analysis of ductile fracture initiation, local approach can be used for stable
crack growth modelling. In case some of the uncoupled micromechanical models are
used, crack growth can be modelled using the node release technique, controlled by the