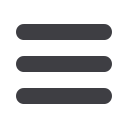
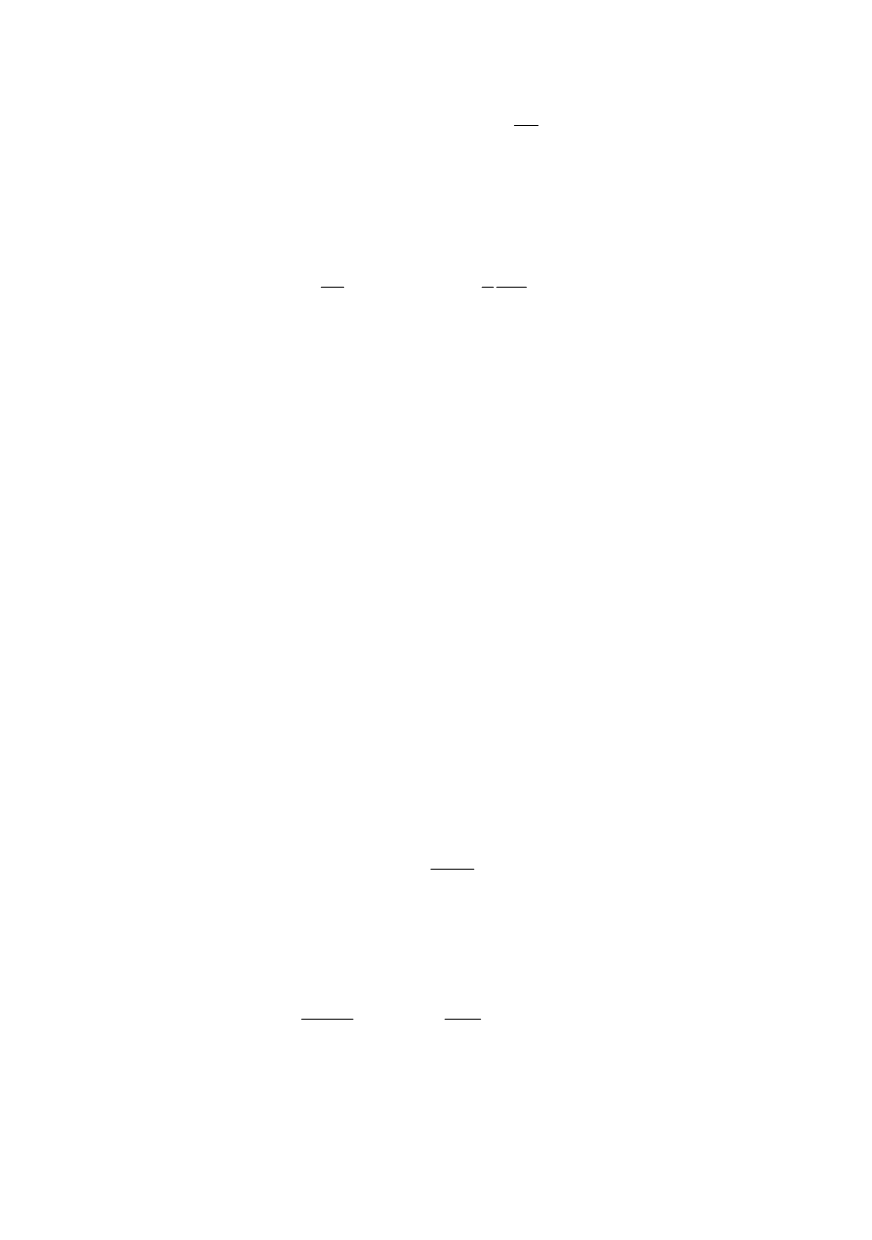
71
0
3
p
eq
p
d
eq eq
m
dR
W
d
R
ε
σ
ε
σ
⎛
⎞
=
+
⎜
⎟
⎝
⎠
∫
(4)
As already mentioned, one of the problems in application of the uncoupled approach is
the treatment of the final stage of damage until the final failure. Beremin research group
/3/ proposed a rather simple way to define the failure criterion, by integrating Eq. (1)
from zero to the experimentally determined strain at fracture
ε
f
:
0
0
3
ln
0.283 exp
2
f
p
m
eq
eq
c
R
d
R
ε
σ
ε
σ
⎛
⎞
⎛ ⎞
=
⎜
⎟
⎜ ⎟
⎜
⎟
⎝ ⎠
⎝
⎠
∫
(5)
where (
R
/
R
0
)
c
is the critical void growth ratio. Similar procedure can also be applied to
the expressions of Huang and Chaouadi.
It is very important to choose the appropriate location in the structure where the Eq.
(5) is applied. That should be the critical location (or locations) in a structure, e.g. crack
tip, stress concentrators or regions with high stress triaxiality. The value of the critical
void growth ratio decreases with increase of triaxiality, but this change isn’t significant,
which was a conclusion of the round robin project /7/ dedicated to local approach to
fracture. According to Chaouadi et al. /5, 6/, parameter
W
dc
(critical damage work)
exhibits even less pronounced dependence on stress triaxiality. However, the results
obtained using the parameters
W
dc
and (
R
/
R
0
)
c
do not differ significantly, because the
damage work concept is derived on the basis of the model of Rice and Tracey.
Simple numerical procedure and possibility to use the results of a finite element
analysis for many post-processing routines are advantages of the uncoupled approach,
favourable for engineering assessment /8, 9/. However, significant disadvantages of this
approach are modelling of the final stage of ductile fracture - void coalescence, and
nucleation of so-called secondary voids during the increase of the external loading.
3. MODELS BASED ON THE YIELD CRITERION OF A POROUS MATERIAL
The coupled approaches to material damage and ductile fracture initiation consider
material as a porous medium, taking into account the influence of voids on the stress-
strain state and plastic flow of the material. The existence of voids in the plastically
deforming metallic matrix is quantified through a scalar quantity - void volume fraction
or porosity
f
:
voids
V f
V
=
(6)
where
V
voids
is volume of all voids in the analysed material volume
V
.
Based on the work of McClintock /10/ and Rice and Tracey /2/, Gurson /11/ derived
several models of void-containing unit cells, obtaining the yield criterion of a porous
material that became the basis for many often-used models of coupled approach:
2
2
3
3
2 cosh
1
0
2
2
ij ij
m
Y
Y
S S
f
f
σ
φ
σ
σ
⎛
⎞ ⎡
⎤
=
+
− + =
⎜
⎟ ⎣
⎦
⎝
⎠
(7)
This constitutive equation is based on the assumption that the behaviour of the
material is isotropic - i.e. it can be treated as a continuum “weakened” by the existence of
voids. The parameter
f
is calculated during the processing procedure, because it is directly