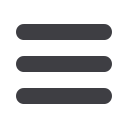
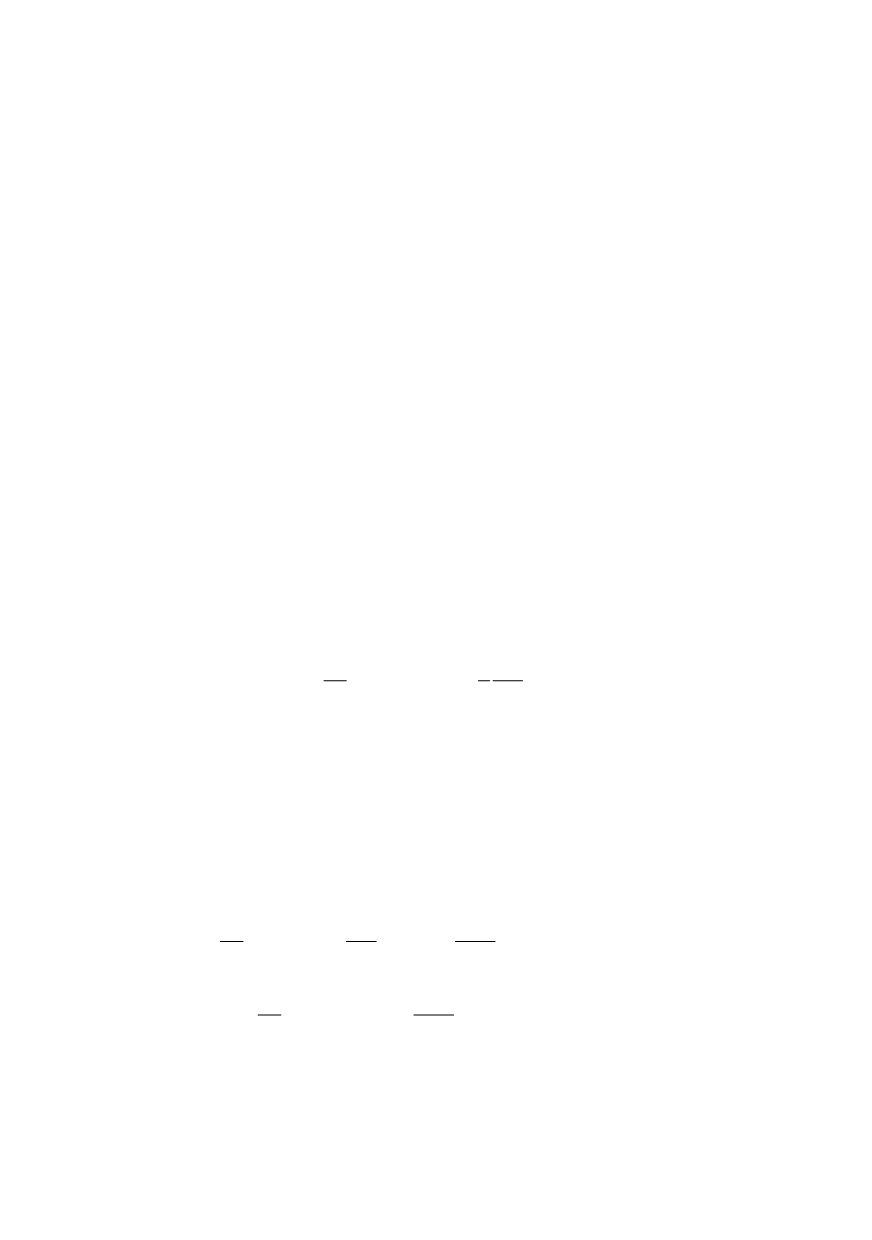
70
quantification are determined locally, the aim is to achieve so-called
transferability
of the
model parameters to different geometries.
As another advantage in comparison with EPFM global approach, local approach can
be used for prediction of ductile fracture initiation in geometries without initial cracks,
because reaching the critical value of the damage parameter will eventually lead to crack
initiation at some critical location - with high values of triaxiality or plastic strain.
Local approach to ductile fracture is used here for assessment of the crack growth
initiation and its stable growth in welded joints made of high-strength low-alloyed steel.
Presented results include the analysis of the influence of the overmatched joint width,
finite element size and formulation and initial crack length on ductile fracture initiation.
2. MODELS BASED ON THE GROWTH OF AN ISOLATED VOID
Uncoupled modelling of ductile fracture is based on the analysis of the growth of an
isolated void in a material under the external loading. Such simplification is appropriate
in case when the number of voids in the metallic matrix during the initial stage of fracture
is small, and the distance between them is large. Therefore, the stress and strain
concentration around the void should not affect other voids.
The assumption of the uncoupled modelling is that the void presence does not
significantly alter the behaviour of the material; for that the damage parameter is not
incorporated into the constitutive equation, with frequently used von Mises plastic yield
criterion. A very important issue is defining the conditions for the loss of load-carrying
capacity of the material due to the damage caused by ductile fracture mechanism.
The model of Rice and Tracey /2/, modified by research group Beremin /3/, states that
the void growth is strongly dependent on stress-field multiaxiality and plastic deformation
of the material:
0
0
3
ln
0.283 exp
2
p
eq
p
m
eq
eq
R
d
R
ε
σ
ε
σ
⎛
⎞
⎛ ⎞
=
⎜
⎟
⎜ ⎟
⎜
⎟
⎝ ⎠
⎝
⎠
∫
(1)
where
R
stands for the actual mean void radius,
R
0
is its initial value,
σ
m
/
σ
eq
represents
the stress triaxiality, and
p
eq
ε
is the equivalent plastic strain. Significant influence of
stress triaxiality on damage parameter and ductile fracture initiation can be seen from Eq.
(1), because the increase of
σ
m
/
σ
eq
directly causes the increase of void growth ratio
R/R
0
.
Another modification of the Rice - Tracey model was proposed by Huang /4/, by
introducing
σ
m
/
σ
eq
= 1 as the limit value for high stress triaxiality and separating the
expressions defining the void growth for the two cases
1/4
0
0
3
ln
0.427
exp
2
p
eq
p
m
m
eq
eq
eq
R
d
R
ε
σ
σ
ε
σ
σ
⎛ ⎞
⎛
⎞
⎛ ⎞
=
⎜ ⎟
⎜
⎟
⎜ ⎟
⎜ ⎟
⎜
⎟
⎝ ⎠
⎝ ⎠
⎝
⎠
∫
for
σ
m
/
σ
eq
≤
1
(2)
0
0
3
ln
0.427 exp
2
p
eq
p
m
eq
eq
R
d
R
ε
σ
ε
σ
⎛
⎞
⎛ ⎞
=
⎜
⎟
⎜ ⎟
⎜
⎟
⎝ ⎠
⎝
⎠
∫
for
σ
m
/
σ
eq
> 1
(3)
Starting from the model of Rice and Tracey, Chaouadi et al. /5, 6/ proposed another
damage parameter for development of ductile fracture in the material -
damage work
,
which is the work due to the plastic deformation, taking into account the change of
volume at the local level around the void. This new parameter can be expressed as: