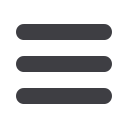
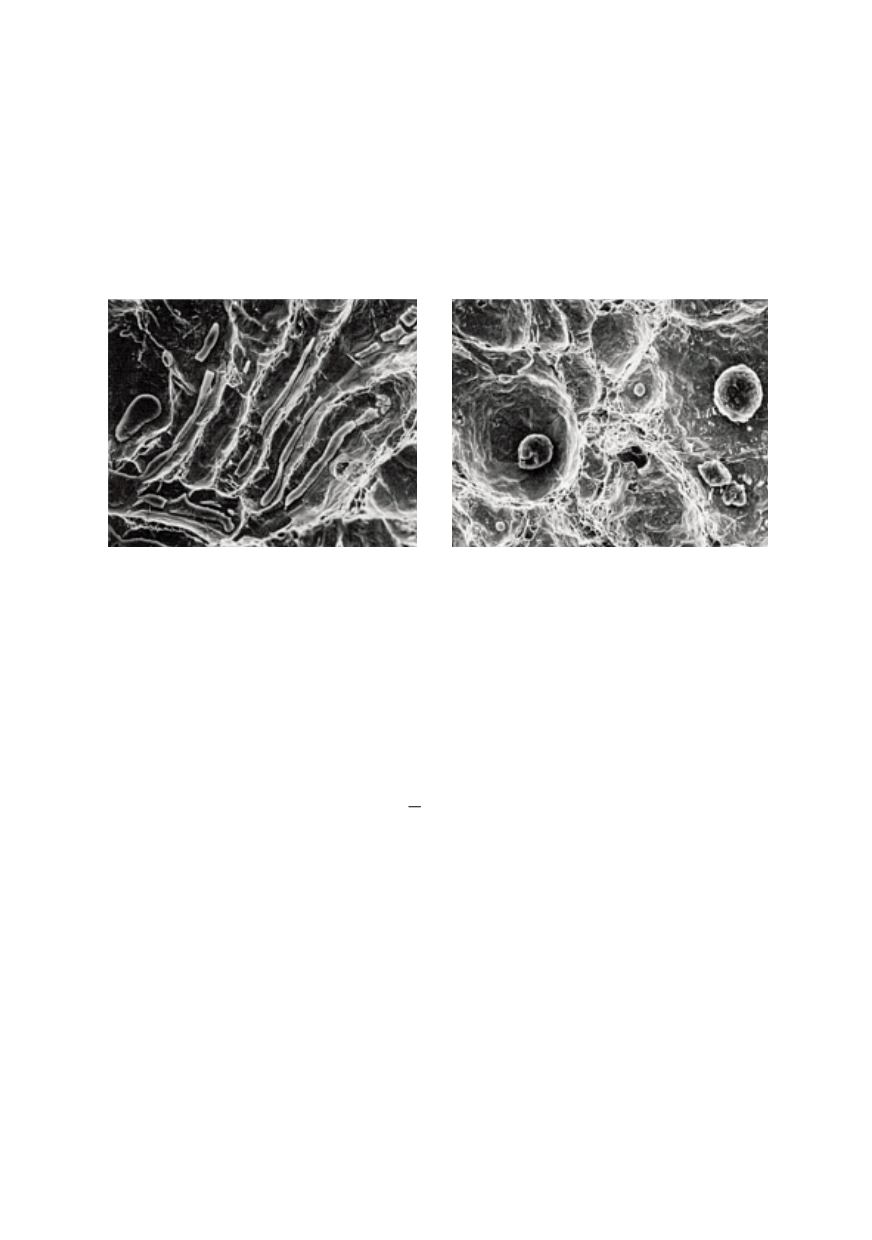
291
beneficial roles of particles. Their beneficial influence was basically oriented in two
directions: (i) grain refinement in as-cast and thermo mechanically treated state /10-14/,
and (ii) nucleation of tough phases during austenite decomposition /15-17/.
The formation of new phases of particles consists of two stages: a) nucleation of new
phases (formation of nuclei) and (b) growth of new phase (nuclei growth) /11,14,17,18/.
The size of the final product depends on the interrelationship between nucleation rate and
growth rate. Therefore, two extreme situations are: (1) high nucleation rate and small
growth rate - leading to very fine microstructure, and (2) small nucleation rate and high
growth rate - leading to very coarse microstructure.
(a)
(b)
Figure 8: SEM fractographs showing the effect of calcium treatment on the fracture morphology of
ASTM A633C steel impact specimens /9/
(a) Untreated steel with elongated manganese sulphide inclusions
(b) Calcium treated steel with spherical inclusions
The nuclei of new phase may be formed in the parent phase by thermally activated
‘random fluctuations’. The stability of such nuclei is dependent on the energy balance
between the volume driving force and the surface energy term. Assuming a spherical
nuclei of radius
r
, an energy balance for the surface energy (
γ
) created and the volume
free energy (Δ
G
v
) change gives /11,14,17,18/
3
2
4
4
3
total
v
G
r G r
π
π
γ
Δ = − Δ +
(2)
The Eq. 2 describes the theoretical possibility for random-homogenous nucleation, i.e.
nucleation can start in any point in volume with equal probability. In real systems, due to
the presence of grain boundaries, surface of the casting mould, inclusions and particles. In
the case of solidification, this equation is modified and new energetic balance is given in
Eq. (3) and schematically shown in Fig. 9 /11,14,17,18/.
total
v
SL SL SM SM SM ML
G V G A
A
A
γ
γ
γ
Δ = − Δ +
+
−
(3)
where
V
is the volume of the nuclei,
A
SL
is the surface (area) on the interface liquid/solid
and
γ
SL
is surface energy on interface liquid/solid,
A
SM
– is the surface (area) on the inter-
face mould/solid and
γ
SM
is surface energy on interface mould/solid,
γ
ML
is the surface
energy on interface liquid/mould, and
θ
is the wettability angle (9).