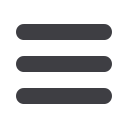
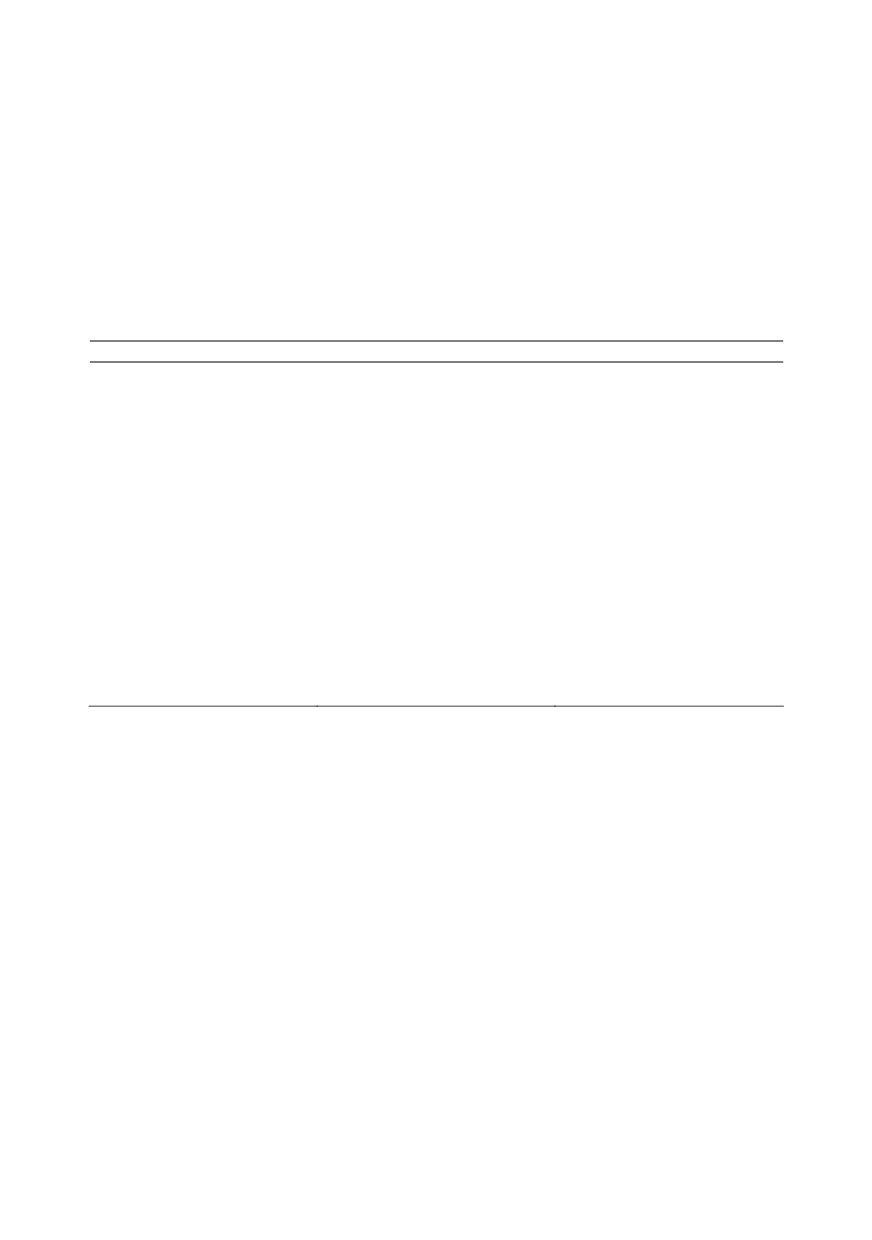
11
(
)
/
23.2 for Nb
m
Q RT
=
(2)
when carrying out the fillet weld, it may be estimated whether or not the NbC is likely to
have gone into solution.
According to the data available, the fillet weld was carried out with a 5 mm covered
(basic) electrode of the type OK 48.30, manufactured by ESAB. The following data for
this electrode is recommended: current 200-260 A, voltage 24 V. Assuming an efficiency
of 0.8 for MMA welding procedure, an input energy of about 0.7-0.8 MJ m
-1
can be
calculated. This corresponds to a
Δ
t
8-5
of about 2-3s, giving a temperature of solution for
NbC of cca. 1270
°
C
Table 1: Summary of microstructural and mechanical properties of applied base materials
Property
Main bracing
Flange plate
Composition (approx.)
0.17wt%; 0.32 Si; 1.37Mn;
Not specified
0.044 Al; 0.029 Nb
C
equiv
0.41
Not specified
Grain size (normalized)
ASTM 11.5 (ca. 8
μ
m)
ASTM 10.7 (ca. 7
μ
m)
Micro-structural features
1.Banded, ferritic-pearlitic
1.Banded, ferritic-pearlitic
2.Slag content low, mainly
2.Slag content fairly high;
MnS, finely distributed
Mainly MnS in extreme
rolled-out form
σ
y
(rolling direction)
345-353 N mm
-2
Not specified
σ
t
(rolling direction)
506-518 N mm-2
Not specified
σ
t
(transverse direction)
419-474 N mm-2
215-437 N mm
-2
Area reduction (rolling
30-34 %
Not specified
Direction)
Area reduction (transverse)
6-13 %
1-7 %
Impact strength (Charpy)
0ºC
83 J
Not specified
-40 ºC
36 J
16 J
The implications of this are threefold. In the first place, it means that grain growth in
the HAZ at temperatures above ca. 1270
°
C can occur. In addition, it is likely that Nb in
solution tends to promote the lower transformation products on cooling. Finally, the very
rapid cooling rate through 800-500
°
C predicted for this welded joint (
Δ
t
8/5
=2-3 s) tends to
promote the martensite transformation in this steel.
Taking into account estimated cooling time and peak temperature, it can be predicted
that the maximum austenite grain size for this weld energy-input (assuming a thick-plate
condition) is of the order of ca. 30-35
μ
m, compared with ca. 8
μ
m for the ferritic base
material. Thus, the Nb in solution in the region of the HAZ and the high cooling rate are
both likely to produce a hard bainitic - martensitic microstructure in the HAZ of the
bracing material. The conclusion is supported by the hardness measurements (Fig. 7)
carried out on the fillet weld in question.
The presence of a number of small, underbead cracks in the vicinity of the HAZ of the
fillet weld in the bracing material is intriguing, primarily because of cold cracks. The use
of a basic electrode should normally keep the hydrogen content at a low value. On the
other hand, it has been well established that the stress concentration at the weld was likely
to be high and the microstructure is likely to contain martensite. On this basis, cold cracks
of the fillet weld cannot be ruled out, even in the presence of low hydrogen levels.