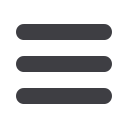
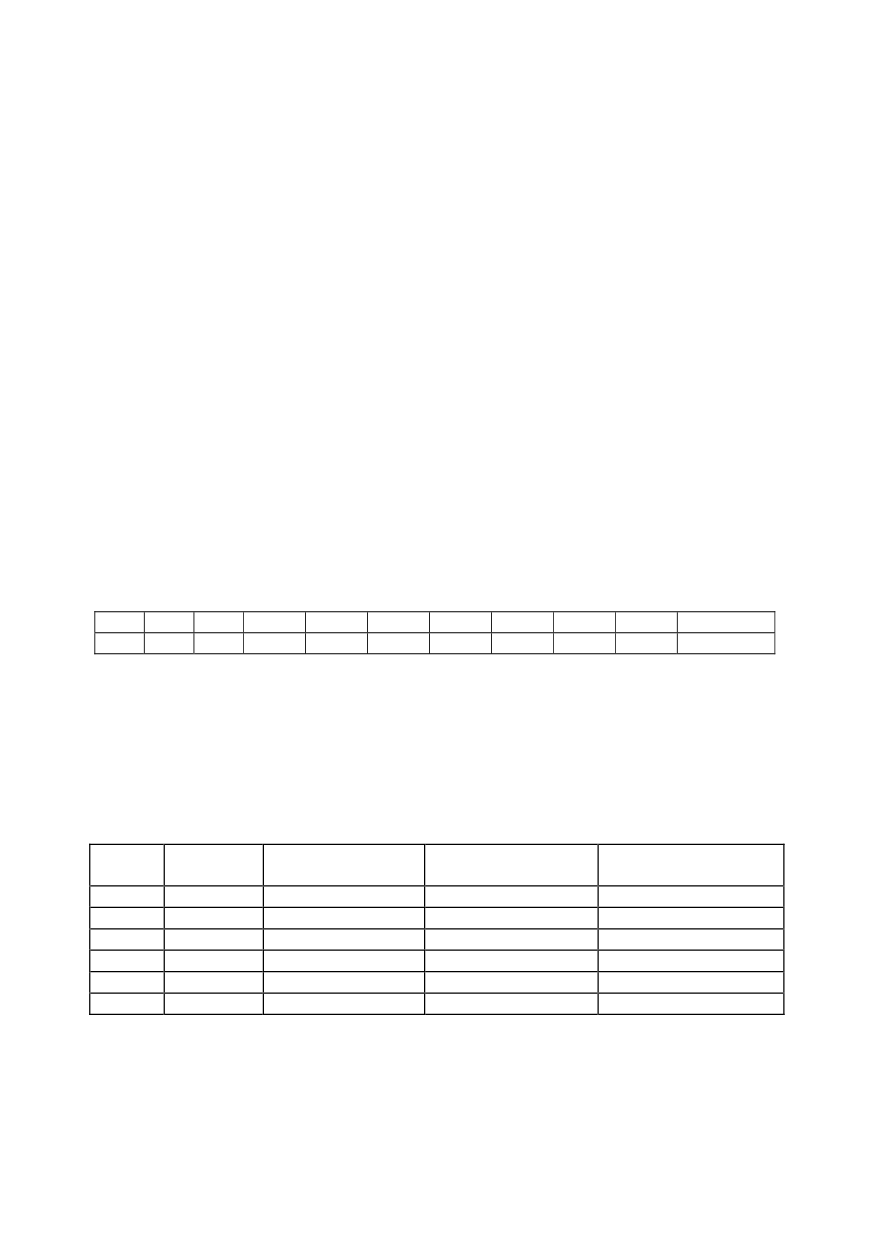
14
The following action had been performed:
1. Investigation and analysis of the causes of wheel fracture.
2. Establishment of the crack growth rate brought about by material fatigue. Assessment
of whether the cracks could have been detected before fracture (during routine inspection)
is based on this.
Parts of fractured wheel, i.e. sample taken from the fractured zone, were used for
fracture investigation and analysis. The wheel material sample was also used to determine
the crack growth rate during fatigue stressing.
3.1. Fracture analysis
A sample for fracture analysis had been taken from UV 7929/114 wheel. Visual
inspection gave the following results:
- a 14x35 mm fatigue caused crack was noticed in the lower left corner on the wheel rim;
- ridges (scores) in the rest of the rim and flange (directed toward the fracture source, i.e.
fatigue crack), as typical signs of brittle fracture;
- traces of plastic deformation on the wheel tread surface.
Part of the fracture surface is examined by a scanning electronic microscope (SEM) in
order to detect possible material texture faults and to examine fractured surface in detail.
This examination failed to reveal any fault.
Chemical analysis was performed by an ordinary wet process, and results are shown
here in Table 2. It is clear from the results that the composition is in accordance to UIC
812-3, Table 2 regulation (R7T Steel).
Table 2: Chemical composition of wheel sample
C
Si
Mn
P
S
Cr
Cu
Mo
Ni
V
Cr+Mo+Ni
0.53 0.36 0.72 0.021 0.022
0.18
0.24
0.03
0.06
0.03
0.27
3.2. Mechanical properties
Impact toughness was tested on Charpy pendulum machine using standard V2-notched
specimen. Total energy was separated into the crack initiation and crack growth energies.
The specimens were sampled in two directions, transversal and longitudinal in respect
to wheel circumference. The results, presented in Table 3, reveal low impact toughness
values, especially low crack growth energy.
Table 3: Results of impact tests performed on Charpy Pendulum machine
Sample Specimen Total impact energy
E, J
Crack initiation energy
E
inic
, J
Crack growth energy
E
growth
, J
U1
1
19,0
18,1
0,9
U2
2
14,4
13,7
0,7
U3
3
18,5
17,2
1,3
P1
1
15,8
14,5
1,3
P2
2
15,8
14,7
1,1
P3
3
17,7
16,2
1,5
3.3. Material fatigue test
Fatigue testing was performed in accordance with ASTM E647 Standard, by three
points bending of standard Charpy specimens, on a Resonating High-Frequency Pulsating