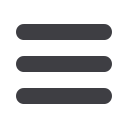
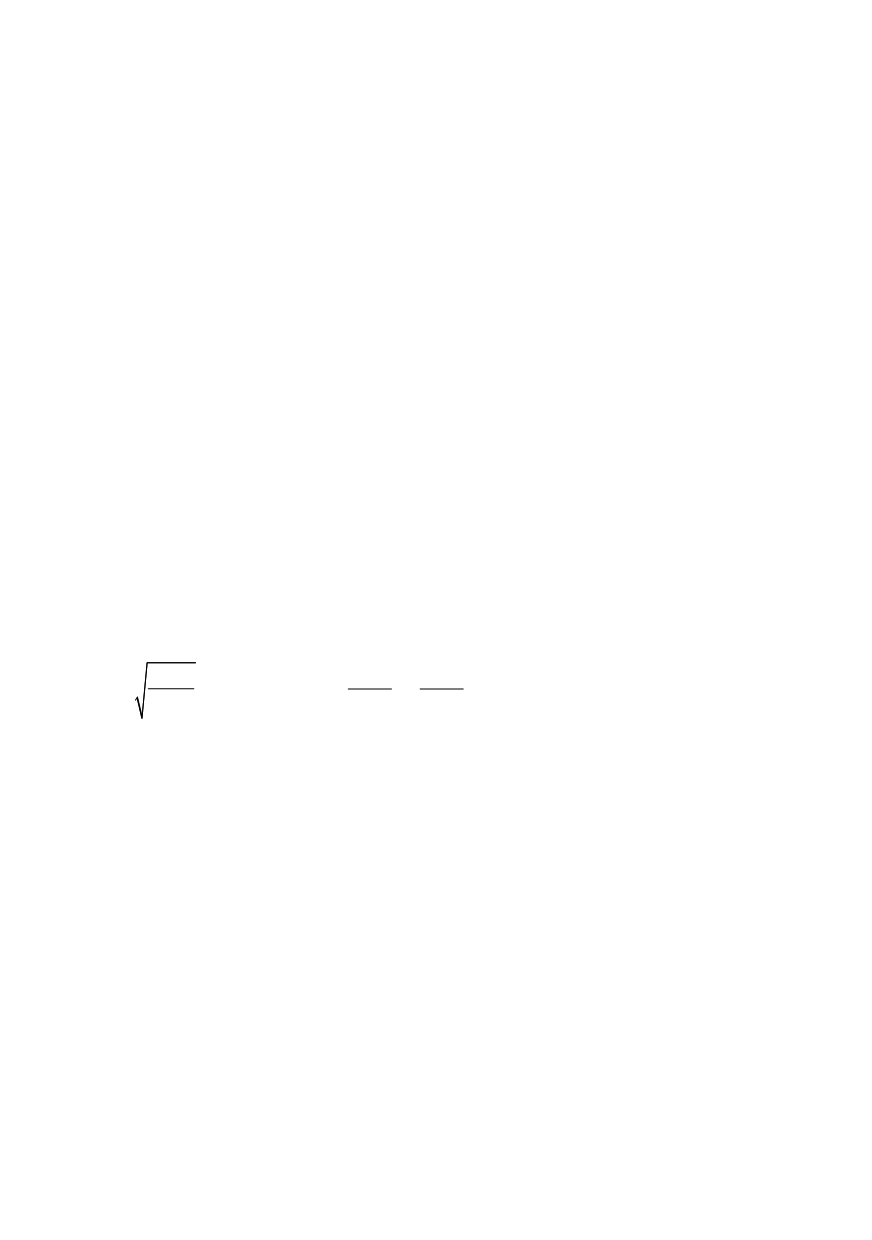
131
precede the leakage, since it is difficult to detect them. Apart from this, surface cracks are
space (volume) cracks, what means that the relationships are complex. Numerical investi-
gations have shown not only the increase of
J
-integral due to the plasticity but also
redistribution along of the crack contour compared to the linear elastic solution. Since the
constraint is near to the crack tip weaker, material is here more liable to the yielding. By
it, based on redistribution, the conditions inside of the crack surface get worse, and this
can lead to the accelerated breakage in this part of the crack. Significant differences in the
behaviour compared to the through crack require the application of material of special
characteristic, but the use of such materials is due to the significant dependence on
geometry and test conditions unreliable.
The aim of the problem for surface crack in space treatment, starting from the fact that
for the fracture assessment under plasticity conditions, both the stresses and strains must
be considered, new method has been developed by the author, already presented at
previous IFMASS’s. This approach will be presented here by the design of Fracture
Analysis Diagram (FAD). The FAD application, which combines the corresponding
criteria of pure brittle and pure plastic fracture, although of different origin, is included in
many codes, like in R-6, API 679, BS 7910 and SINTAP. Differently to classical form of
interpolation between these limit cases, the points of new proposed diagram solution are
calculated starting from the relationship based only on fracture mechanics.
Starting from the known relationship between
J
and
K
that after substitution
ref
J K K
σ
ε
=
(1)
holds its validity in all ranges between elastic to the plastic, it follows, in the design of
FAD, for an engineering material stress-strain curve described in form
(
)
n
F pl
B
σ
ε
= Δ
r Y
r
ref
L K
E
σ
ε
=
with
1/
n
r Y
r Y
ref
F
L
L
E B
σ
σ
ε
⎡
⎤
⎛
⎞
⎢
⎥
=
+ ⎜
⎟
⎢
⎥
⎝
⎠
⎣
⎦
(2)
On the basis of given relationships the curve in Fig. 6 is designed. For the comparison
the curve obtained with R-6 method using the same material properties is presented.
Noticeable is considerable difference between the two lines. This is not surprising,
having in mind that the R-6 curves is designed with the idea „safe rather than accurate“
(and to avoid possible errors on the side of lower safety).
The resistance curve path shows that up to the stress level in cracked cross section
(net-section) at 70 % of the yield strength the available plasticity is sufficient to held, on
the basis of crack tip blunting, the material resistance at the same level as without crack.
After that the plasticity starts to be consumed through the deformation in the volume
outside of the crack, and this act negatively to the residual strength.
The accuracy of the calculation based on new method is verified through the series of
test on surface crack specimens and massive cylinders with the equal wall thickness and
crack size (Fig. 7). Comparison with the results obtained by R-6 (Fig. 8) convincible
demonstrates the advantages of new method not only due to the simplicity but also
regarding the reliability. Details of the calculation by new method are given in /3 to 7/.