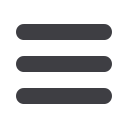
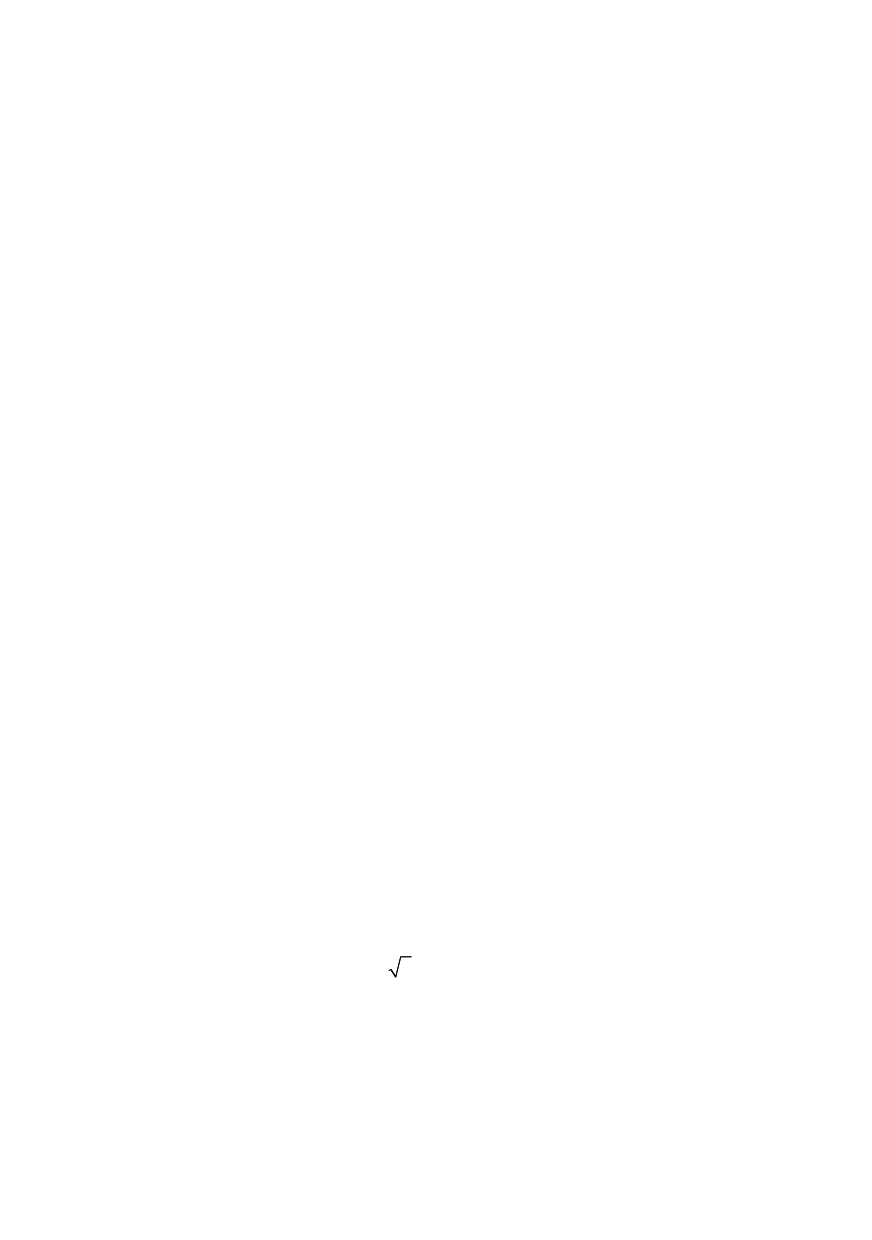
128
Not only that this treatment is desirable for the unification, but this will lead to the
more direct and less exposed to the errors, consideration of the corresponding conditions.
But, when the reduction of the section due to the crack is significant, the application of
the values calculated for remote section without crack is risky, since is not on the safe
side. This is significant in Elastic-Plastic-Fracture-Mechanics (EPFM), because the plas-
tic effect in the section reduced by the crack occurs earlier, with very high intensity.
Researches in EPFM range were very successful by establishment of the parameters
that characterise process of ductile fracture. The experimental methods adequate for the
evaluation of fracture resistance and analytical methods for the fracture conditions have
been developed. However, the corresponding methods require very complex analyses that
can be conducted only with the help of advanced finite element methods, what can be
expensive, time consuming and require high level of corresponding skills for the
realisation. That certainly represents one of main obstacles to the extension of the EPFM
methods for the structural integrity evaluation.
To overcome these obstacles, that additionally reduce general applicability of EPFM,
so-called engineering approach (like that developed by EPRI) is developed for use, also
based on simplifications which require no finite element analysis and in this way make
this kind of analysis attainable to the engineering community. Unfortunately, application
of this method is also followed with the limitations and the question arose whether it is
superior knowing the current level of finite elements methods and computers capacity.
Looking on the different solutions for the calculation of crack parameters (
K, J
), it is
to notice that cracks always have an ideal form. Natural defects are not of such a form
and their contours are usually irregular and for that they cannot be examined by standard
procedures. On the other hand, it is well known that these defects after growth under
fatigue loading gradually convert into the typical semi-elliptical form. Based on this, the
procedure is developed assuming that all natural defects are of simple form of plane or
elliptical contour, convenient for next consideration. Certainly, the idealized or effective
cracks are not real cracks, but only simplified representation of their complex real form
enables their treatment by the fracture mechanics procedures.
Rules for this idealization (so-called reconsideration) of real cracks are developed in
details from different codes. In Fig. 3 is, as an example, shown one method of treatment.
The trend with this is obvious, that end forms are on the safe side, although there is no
definite evidence in this respect. Initial natural defect is in all cases completely contained
in the new effective contour, whose area is then larger.
Necessity to use finite elements, particularly in EPFM, has been several times already
emphasized. Also in this area different simplification were necessary to enable the
simulation of condition at the crack tip. For the adequate calculation of stresses and
strains with the help of finite elements it is necessary to reproduce corresponding
singularity in accordance with the theoretical solution of fracture mechanics. As known
there are two tips of singularity;
1 /
r
for elastic material behaviour, and
r
-n/n+1
for
elastic-plastic material, whose behaviour is described by the exponent relationship. In the
last case, by elastic perfectly plastic materials (
n
→ ∞
) the singularity takes value
r
-1
.
Besides, the changes in the crack tip geometry due to blunting must be taken into account.
The field of deformations is modelled by the polynomials using standard finite
elements, and with those elements modelling of singularity is not possible. Therefore
simple conventional elements cannot be used for crack modelling.