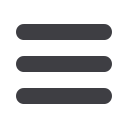
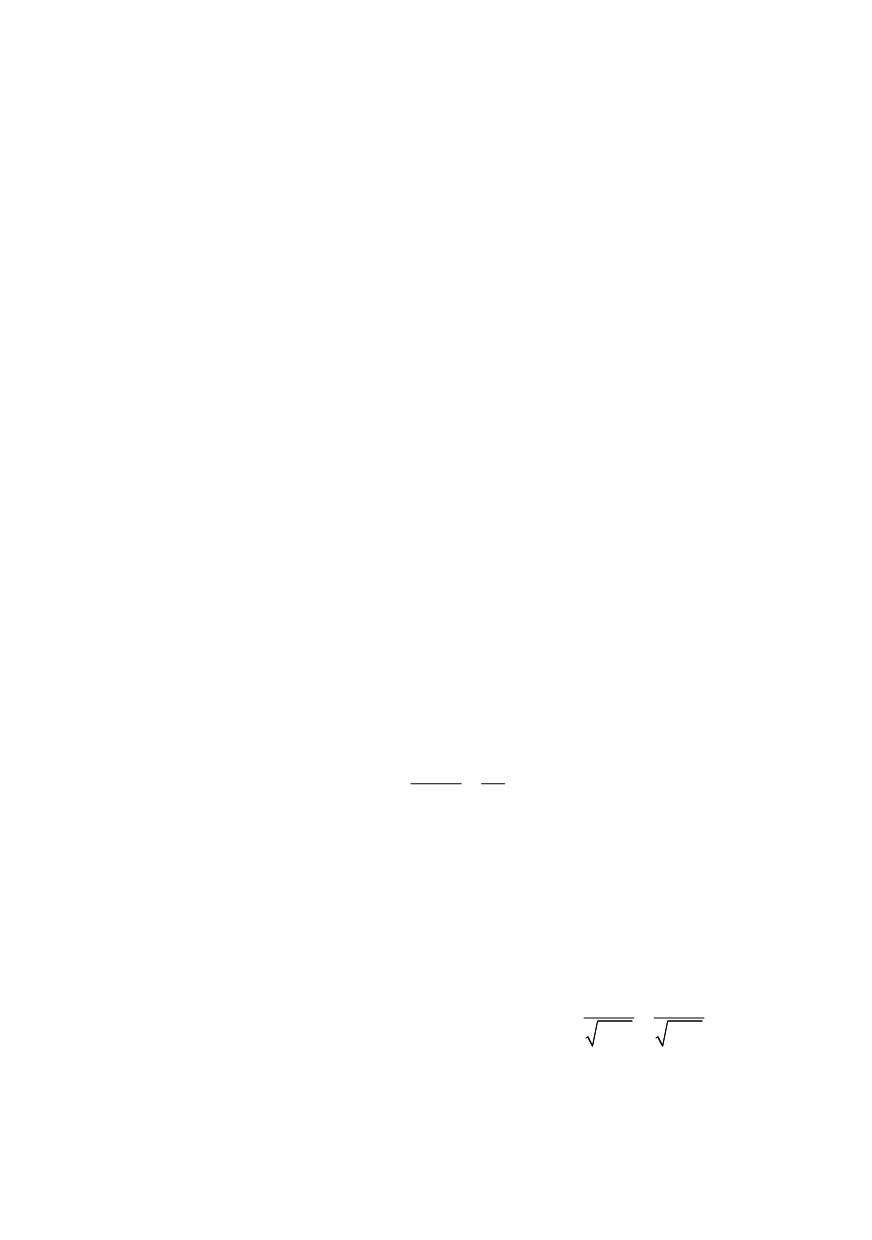
137
Proof test can be applied as the alternative for non-allowed crack detection (for
example, if the complex component form do not allow efficient NDI application), but also
as additional mean to the NDI. The reliability of components will be certainly increased
by the strategy of combined inspection using both proof test and NDI. NDI can bi carried
out with this before or after the test. NDI before test has advantage since it reduce the risk
of failure during test, and when the position of the crack become in this way known, its
evaluation and calculation difficult, it is possible to measure the crack opening and
possible growth during the test using gauges (Fig. 13) for control and prevention of
fracture during test. If the NDI is executed after test, crack detection is significantly
improved because crack opening based on its blunting.
Finally, proof test opens the possibility of stress measurements during test for testing
of calculated values. This is very important, because the accurate evaluation of stresses
under operational conditions for the accurate evaluation of fracture mechanics behaviour
and prove of structure reliability is necessary. Consequently, the most important by the
proof test project is, beside the fracture avoidance through the overloading, to avoid the
non-necessary permanent damage of component. Damage can appear during test from
many reasons. For example, if the test is performed under the conditions that material is
regarding toughness significantly weaker than under the service conditions, the crack can
develop (due to overloading) even when it would be not appear under normal conditions.
More frequent failures in test can emerge if the
a
0
size is small compared to the typical
manufacturing defects. Accordingly, although conditions tightening and increase of proof
test numbers may increase reliability in service of structures that survived this test, this
may unnecessary increase fractures during test by the cracks, smaller than cracks growing
up to the critical size for the fracture in service. The optimisation is here necessary.
Projecting of proof test is serious task and it is only possible based on detailed
investigation of design, its loading and operational conditions. Since the calculation of
pressure containing components is usually based on more complex methods, e.g. finite
elements, for pipes simplified methods are often applied. The widely used formula for the
evaluation of pipe bursting pressure (plastic collapse) of wall thickness
h
through axial
crack is
F
B
kr
m
h P
P
m R m
σ
⋅
=
=
⋅
(3)
Here
R
m
is the mean pipe radius and
σ
F
flow strength, based on yield
σ
R
and fracture
σ
K
strengths
.(
)
F
R K
k
σ
σ
σ
= +
(4)
Experimental values for
k
vary between 0.5…0.6. At high temperatures, where the
strain hardening is lower, this value tends to 0.5.
Pressure necessary for unflawed pipe bursting is marked as
P
B
, and the required
correction
m
due to the presence of crack is
0.614 0.481 0.386exp( 1.25 )
m
λ
λ
= +
+
−
1/4 2
1.82
12(1 )
m
m
c
c
R h R h
λ
ν
⎡
⎤
= −
=
⎣
⎦
(5)
with
2c
axial length of crack and
λ
as pipe shell parameter.