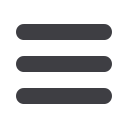
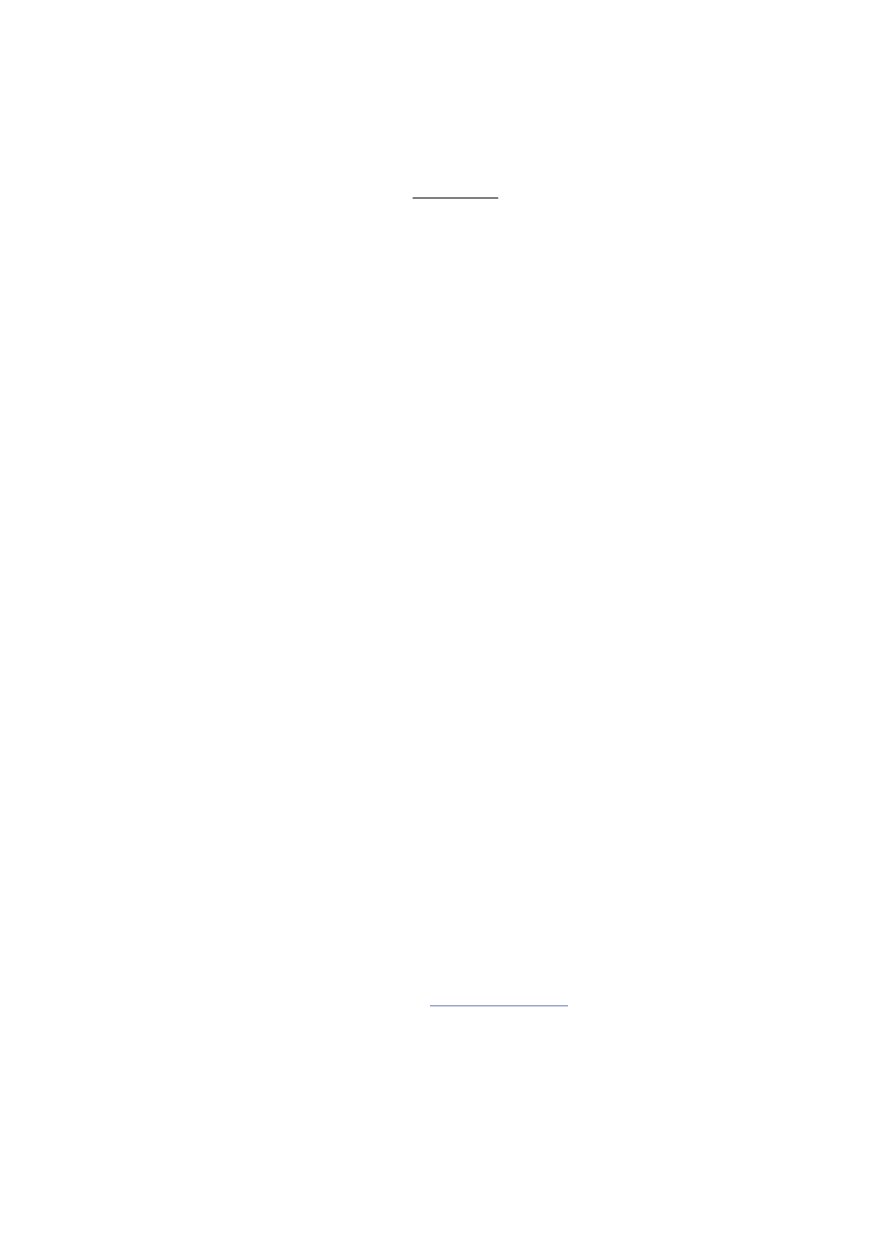
124
Loading path = Crack driving force:
( )
2
e
r
J J f L
−
⎡
⎤
= ⎣
⎦
(25)
(
)
2
I
e
K a, F
J
E'
=
(26)
Limit toughness:
J
mat
Failure criteria:
J
mat
<
J
6. Conclusions
Basic principles of structural integrity assessment have to be taken into account
already in the design stage of a structure. Available procedures enable reliable usage of
fracture mechanics to assess the component integrity. SINTAP, as one of a most
comprehensive assessment procedure, uses the basic principles of R6 and ETM. Integrity
assessment is based on the estimation of maximum allowable loading or maximum
allowable crack size in unfavourable crack tip location and orientation. This lecture gives
the basis of procedure for design against fracture not only in-service, but also in design
and manufacturing phases.
REFERENCES
1.
ASME, 1998,
"ASME Boiler and Pressure Vessel Code, Section XI: Rules for In-service
Inspection of Nuclear Power Plant Components"
, American Society for Mechanical
Engineering
2.
ASTM E 1820-99a, 2000,
"Standard Test Method for Measurement of Fracture Toughness"
,
Annual Book of ASTM Standards
3.
BS 7448, 1997,
"Fracture mechanics toughness tests; Part 2. Method for determination of K
IC
,
critical CTOD and critical J values of welds in metallic materials"
4.
Eurocode, 1993,
"Design Manual for Steel Structures and Building"
, Brussels
5.
BS 7910, 1999,
"Guide on methods for assessing the acceptability of flaws in fusion welded
structures"
6.
API 579-1/ASME FFS-1, 2007,
"Fitness-For-Service"
, Second Edition, American Petroleum
Institute, Washington, D.C.
7.
R5, 2003,
"Assessment Procedure for the High Temperature Response of Structures"
, Issue 3,
British Energy
8.
R6, 2003,
"Assessment of the Integrity of Structures containing Defects"
, Revision 4, British
Energy
9.
SINTAP, 1999,
"Structural Integrity Assessment Procedure"
, Final Revision. EU-Project BE
95-1462. Brite Euram Programme
10. Schwalbe, K. H. and Zerbst, U, 2000,
"The Engineering Treatment Model"
, International
Journal of Pressure Vessels and Piping, Volume 77, Issues 14-15, 2000, pp. 905-918.
11. FITNET, 2006,
"European Fitness for Service Network"
, Final technical report, GTC1–2001–
43049, Contract No. GIRT-CT-2001-05071,
www.eurofitnet.org