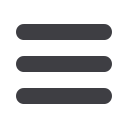
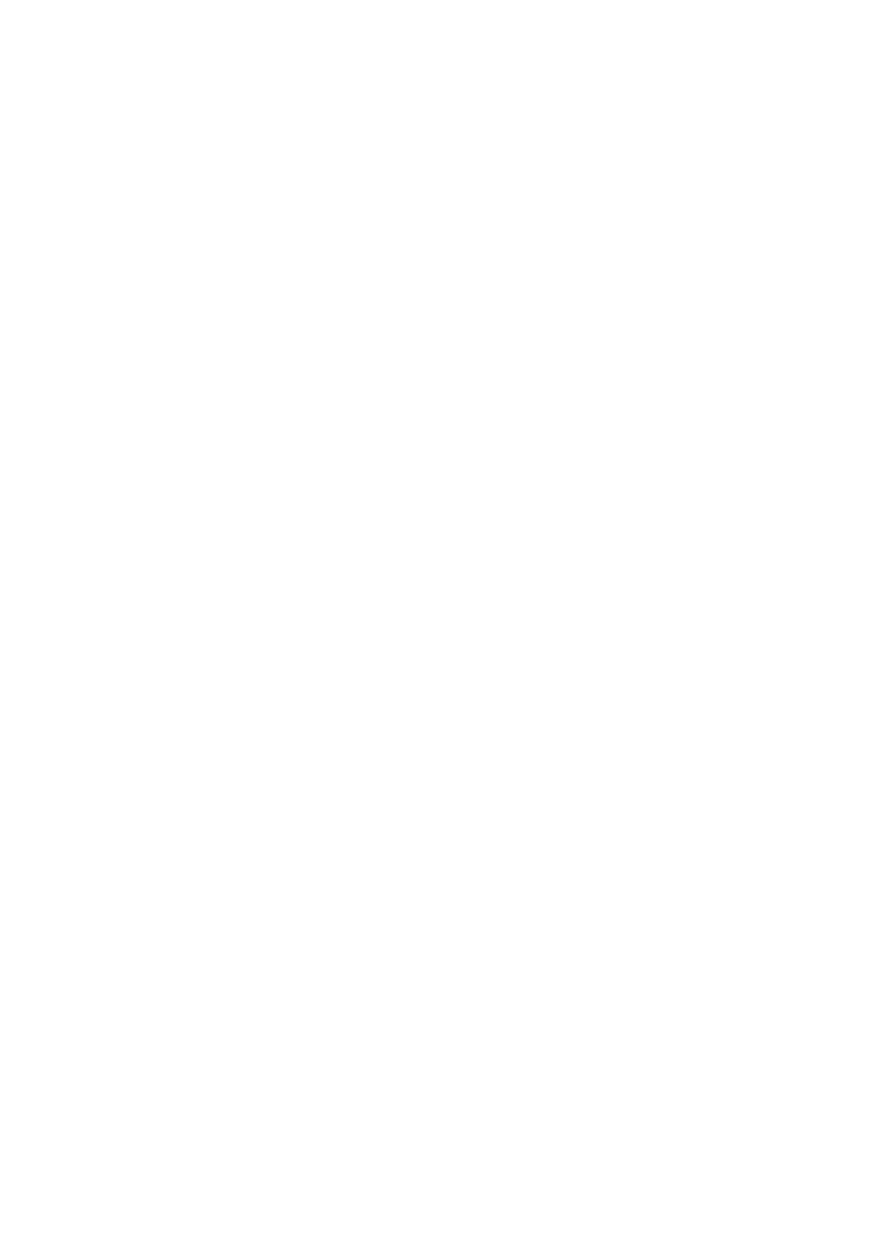
298
2. MARTENSITIC STEELS
The demand for higher efficiency in fossil fired power plants lead to the development
of new creep resistant materials during the last decades. They made it possible to increase
the steam temperature up to range of 625°C for permanent service, using ferritic and
martensitic materials.
Special attention was paid to the improvement of 9-10% Cr-steels martensitic steels.
These grades had their basis in the well known grade T/P9 (X11CrMo9-1). As the next
step forward, T/P91 (X10CrMoVNb9-1) was developed in the 1980
th
. To enhance its
creep-rupture strength, the elements V, Nb and N were added to the alloy of T/P9.
During development of new base materials it is of great importance, that
corresponding filler metals with matching creep strength properties will be developed
simultaneously. Concerning the alloy concept, it is the easiest way that the chemical
composition is identical to those of the base material. That is true for a great number of
filler metals but not for all. Additional micro alloying elements and specialities
concerning improvement of weldability and handling are the detailed knowledge of the
individual development departments. Matching filler metals are developed for common
used welding processes like GTAW, SMAW and SAW, /7/.
The martensitic steels are welded in the “martensitic range”, this means preheat- and
interpass temperatures are between 200°C and 300°C. Due to the martensitic structure
and the required toughness, great care is necessary during welding, regarding the
thickness of individual weld layers, heat input and later with the post weld heat treatment
(PWHT). In all cases, PWHT has two means: tempering and stress-relieving.
Rupture stress increases with preheat and interpass temperature. Since the problem
arises from the heterogeneous microstructure of the HAZ it can be eliminated by a
reaustenitisation and tempering heat treatment.
The problem of tempering during PWHT is to insure safe service conditions.
Appropriate temperature of PWHT lasting for example 8 to 10 hours, permits to maintain
the tensile properties above the requirements and gives toughness values at a high level at
low temperatures.
Pure martensitic transformation result from wall thicknesses up to about 80 mm fol-
lowed by air cooling and begins at temperatures about 400°C. With greater wall thickness
ferrite and carbide will be formed due to the longer cooling periods. At these thickness
accelerated cooling is necessary to maintain a pure martensitic structure. This is valid for
P91, E911 and P92. After welding a PWHT is carried out at 760°C. Here after hardness is
approximately 250 HV 10. The low hardness in these steels is caused by the reduced C
content in P91, P92 and E911 (compared to X20) and it makes further processing easier.
Directly after welding, the hardness in the weld metal is with approximately 400 HV 10
about 100 units below the hardness of the weld metal for X20. Therefore the risk of cold
cracking is reduced, so that after welding and before PWHT, cooling down to room
temperature is possible. It is important that the weld cools completely below martensitic
temperature before heat treatment. This is to achieve total post weld tempering of all
martensite through the ensuing heat treatment. The martensitic finish temperature (
M
f
) of
P91, P92 and E911 is in the range of 150°C, so that cooling to at least 100°C is required.
In dependence of the temperature during PWHT the toughness level can be influenced as
a function of the holding time. The recommended temperature for these grades is 760°C,
but under certain conditions, e.g. for dissimilar joints, a lower temperature could be
necessary. In this case a longer holding time will compensate the lower temperature /7/.