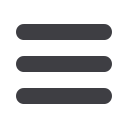
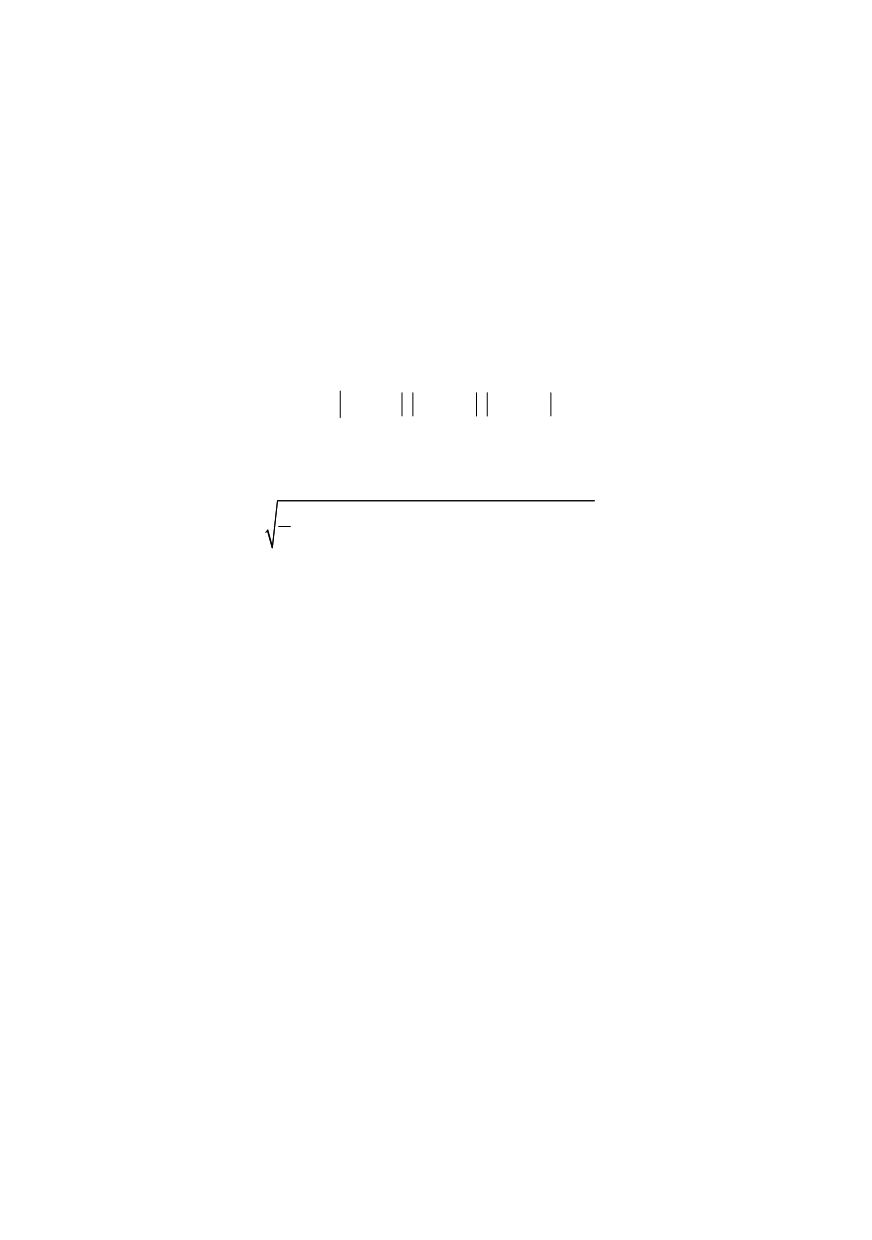
22
The conditions defining growth of plastic strain through the yielding surface, with the
parameters
k
and
α
defining its size and position in stress space are shown in Fig. 3, so
that variation of them allows different kinds of material behaviour to be described.
Accordingly, any change in inelastic strains depends not only on stress state but also
on yield surface, which defines the state of the material and varies as the inelastic strain is
generated. This point out to the fact that the development of inelastic strains is always
accompanied by a change in the microstructure of the material, causing the change in the
material response, including the fracture mechanics parameters.
There are many different criteria which define yield surface change, as the main
conditions for the origin of inelastic strains, but for the purposes of the fracture mechanics
the criteria von Mises and Tresca are generally used.
A Tresca or maximum shear stress criterion is based on the observation that the
materials fracture in shear planes, what is suitable for the application to metals.
{
}
( )
1 2 2 3 3 2
( , ) max
,
,
0
ij
p
YS p
f
σ ε
σ
σ
σ
σ
σ
σ
σ
ε
=
−
−
− −
=
(5)
Von Mises criteria, also named maximum distortion energy criteria, takes in conside-
ration that the hydrostatic stresses in material doesn’t affect yielding and doesn’t partici-
pate in fracture, what is an important characteristics of materials, particularly metallic.
(
)
(
)
(
) (
)
( )
2
2
2
1 2
2 3
3 1
1
,
0
2
ij
p
YS p
f
σ ε
σ
σ
σ
σ
σ
σ
σ
ε
⎡
⎤
=
− + − + −
−
=
⎢
⎥
⎣
⎦
(6)
In both criteria for
(
)
,
0
ij
p
f
σ ε
<
the material deforms elastically, for
(
)
,
0
ij
p
f
σ ε
=
plastically.The yield stress
σ
YS
may increase during plastic straining, as a function of a
measure of total plastic strain
ε
p
. Experiments have shown that if a solid is plastically
deformed, unloaded, and again re-loaded to produce next plastic strains, its resistance to
plastic flow will be increased by strain hardening. So, if the inelastic deformation leads to
the material hardening, than the yield surface increase or move in the stress space.
Obviously, it is possible to describe strain hardening in an appropriate way by
definition how, depending on plastic strain, the yield surface changes its form and
position. Previously described way of yield surface size increase is so called isotropic
hardening, which however, is not adequate for the application in case of cyclic loading,
because it does not account for the Bauschinger effect; that is the hardening by the
loading in one direction has the consequence of softening if loaded in opposite direction.
In this case the application of so-called kinematic hardening is more appropriate, by
which the yield surface moves in load direction without size change.
However, material behaviour in the case of cyclic loading is much more complex and
under elevated temperature further complicated by time dependent inelastic strain (creep).
Let us look back on the flow rule. If the stress state is on the yield surface, and stress
slightly increases, this rule defines direction and size for the development of plastic strain
increment. As already stated this increment only appears for loading increase. Since the
plastic strain increment is dependent on total stress and not on stress increment. this
theory is known as incremental theory of plasticity or flow theory. During loading the
stress follows non-linear line (Fig. 4), and in case of unloading the strains are elastic.
For the purposes of fracture mechanics the theory of non-linear elastic deformation
(deformation theory), by which loading and unloading follows the same curve, is