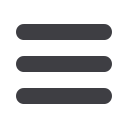
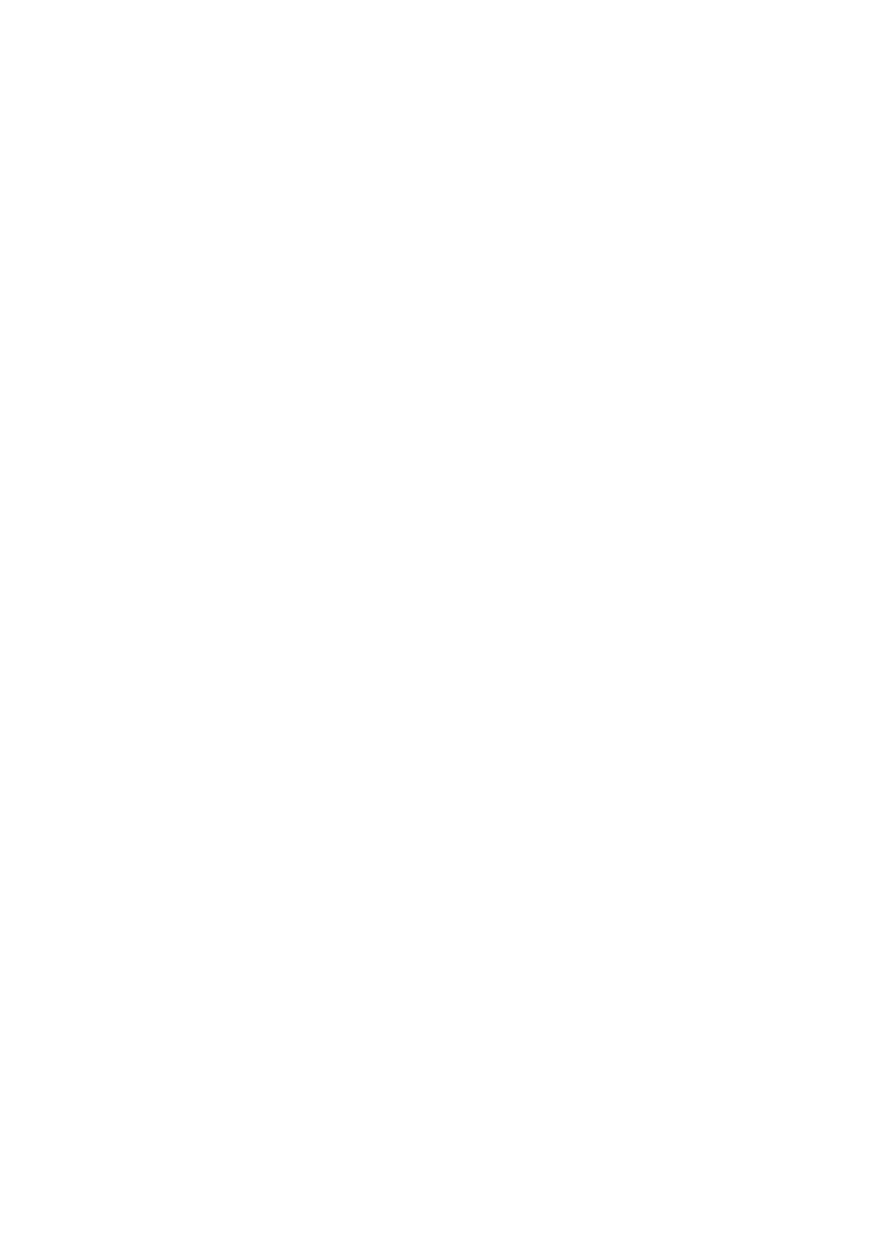
18
- Fatigue crack propagated under the influence of the same cyclic-stresses. The fatigue
crack growth rate is so high that it is practically impossible to monitor it.
- Unstable quasi-static propagation is caused by maximal tensile stress in a single
braking cycle. The required remote tensile stress level (282.5 MPa) is achievable with the
applied braking system.
The general conclusion based on the above analysis is that in the present combination
of material with low resistance to fatigue crack growth and a braking system producing
high tensile stresses a reliable monitoring of crack growth for fracture prevention is not
possible. High susceptibility to stress concentration of fatigue crack initiation, i.e. a small
number of cycles before crack appearance, indicates a need to avoid wheel fastening by
chucks during machining procedure. The following actions have been recommended:
- change machining practices;
- change braking system; and
- perform a detailed analysis of wheel stress state.
Detailed analysis means the calculation of stress-state caused by mechanical loading
and thermal shocks using finite element analysis, as well as the measurement of residual
stresses by ultrasonic and magnetic methods.
4. FINAL REMARKS
It is clear from presented crack parameters and their application that three aspects
have to involved for the analysis of in-service structural failures: theoretical, numerical
modelling and experimental. The scope of necessary knowledge and skill is large. In
theoretical sense at least mechanics, mathematics, physics, material science, theory of
elasticity, theory of plasticity, fracture mechanics are inevitable. Examples show that not
only basic knowledge, but also skill and experience are required to solve complicated
problems of stress and strain analysis, including simplifications and assumptions which
must be introduced when exact solution is not possible. Finally, all obtained solutions and
results must be verified by experiments, far from being simple, especially in the case of
full scale testing. This is also to add the complex standard testing of cracked specimens
and metallography, demanding in performance and result analysis.
Fracture mechanics and its parameters significantly contributed to improve structure
integrity by crack significance and residual life assessment, but also in design, including
materials properties improvement and development of new materials, /5/.
ACKNOWLEDGEMENTS
The authors gratefully acknowledge the financial support from the Serbian Ministry of
Science under the project OI 144027 “Special topics in fracture mechanics of materials”.
REFERENCES
1.
McEvily, A.,
Metal Failures: Mechanisms, analysis, prevention
, ISBN 0-471-41436-0
2.
Harper, R. F.,
Code of Hammurabi
, University of Chicago Press, (1904).
3.
Easterling, K.
Introduction to the Physical Metallurgy of Welding
2nd edition. Butterworths,
London, (1992).
4.
Report 12-29-12.03/2000:
Report on causes of failure of mono block railroad wheel
, Faculty of
Mechanical Engineering, Belgrade (2000) (in Serbian
Izveštaj o stručnom nalazu uzroka
pucanja monoblok točka na putničkim kolima, ŽTP Beograd
)
5.
Nichols, R. W.,
Use of Fracture Mechanics as an Engineering Tool
, The 1984 ICF Honour
Lecture. Sixth International Conference on Fracture, ICF 6, New Delhi, India (1983).