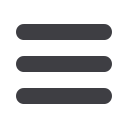
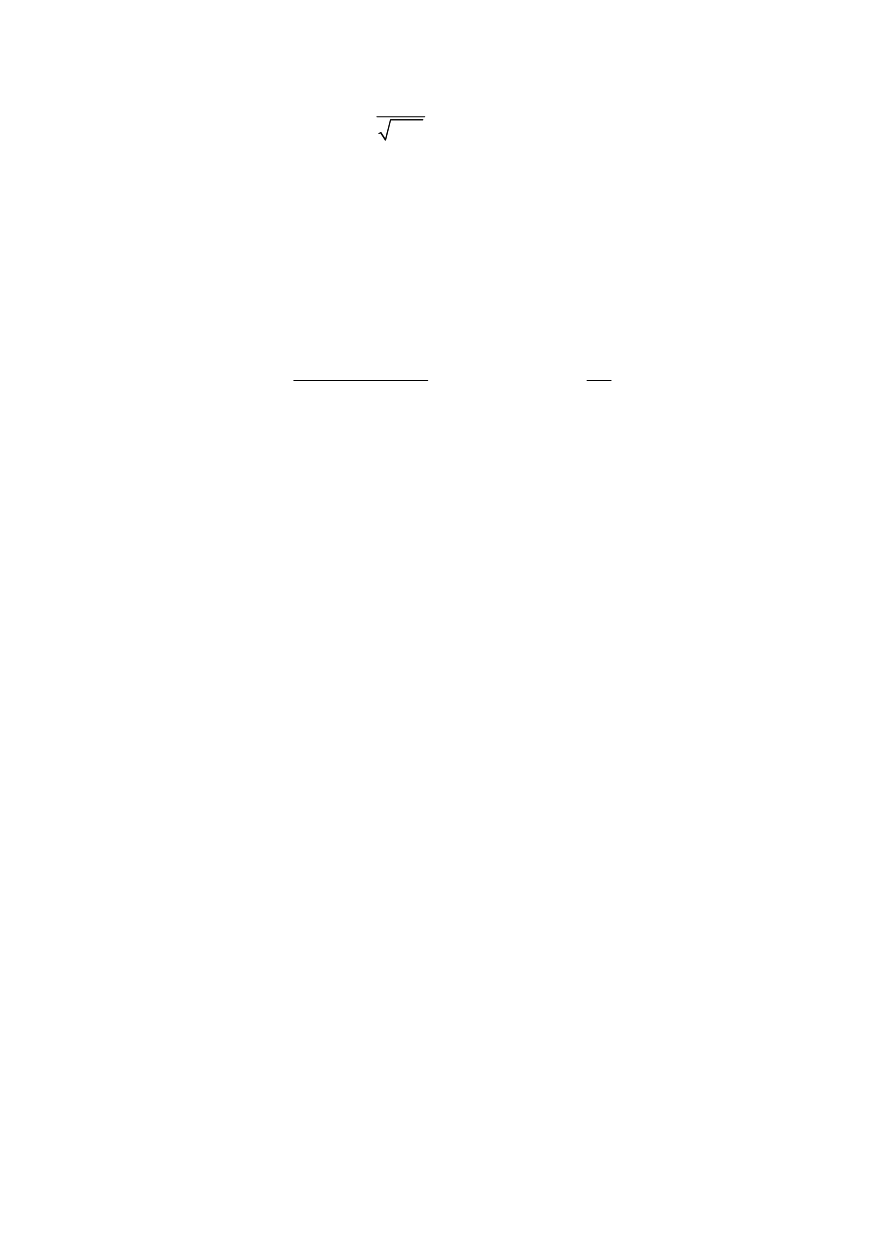
38
( )
2
I
ij
ij
li lj
K f
T
r
σ
θ
δ δ
π
=
+
(28)
T
-stress in the above formula is not singular term, as is the case with the first term
(based on
K
). The
T
-stress, as a homogeneous uniaxial stress field acting parallel to the
crack, obviously increase for small scale yielding (SSY) the constraint, contributing to the
triaxiality of the near-tip region. Also, surprising on a first glance, there is experimental
and numerical evidence that
T
correlates with the constraint effect even for large scale
yielding (LSY). However, based on its origin from the elastic solution the correlation is
only qualitative, and the connection with the
J
- integral solution is not possible.
For the
J
- integral another solution is proposed. The solution is based on Q-factor that
can be evaluated comparing the FEM and HRR solutions for the same case.
(
)
Y
HRR
Q
θθ
θθ
σ
σ
σ
−
=
for
θ
= 0
,
0
2
o
J r
σ
=
(29)
Herein the first is the „real“ stress
σ
θθ
taken from FEM-solution, and second one
which is based on HRR-solution. Distance
r
0
from the crack tip to the calculation point of
this factor is selected to avoid the region of crack blunting where
J
solution is not valid.
Based on (29) it can be also written
(
)
Y
HRR
Q
θθ
θθ
σ
σ
σ
=
+
(30)
With the development of plastic deformation factor
Q
become negative and this means
that the stress values reduce compared to the calculation based on
J
. In general
Q
is a
function of geometry, work hardening, and deformation level. For instance, in the centre
cracked tension geometry
Q
quickly reaches value of 1, whereas, in deeply cracked
bending,
Q
remains close to zero well in the range of general yielding (Fig. 22).
Determination of
Q
is complicated, because it requires a very detailed elastic-plastic
finite element analysis. The most attractive feature of
T
is that it can be determined from
an elastic finite element analysis. Factor
d
n
, appearing in the general relationship between
J
and
δ
(25) is also known to be constraint-dependent, and this means it can serve as a
parameter to characterize constraint. The factor can be determined either by a finite-
element analysis or experimentally. As a displacement-related quantity it is easier to be
determined than the
Q
-factor. Unfortunately, its values can be used only for orientation.
In this field further investigations are necessary. Application of
Q
is not always
successful and, because it requires complicated FEM-calculations, can be the source of
deviation and uncertainties. If this calculation exists, the evaluation of
h
can give the
better survey of general situation of the structure. Moreover, variable calculations at the
same model are accessible for the sensitivity analysis and design optimisation.
5. EPFM PROCEDURES FOR THE INTEGRITY ASSESSMENT
At the beginning it is necessary here to warn design engineers that the characteristics
taken to define strength of materials, like yield strength, tensile strength, elongation at
fracture, do not have nearly anything with the integrity of the structures jeopardized by
the cracks and by the crack growth under service loads.
For many structures and before all for plant vessels and pipes, metal constructions
and
similar
is the application of ductile, yielding materials practical. Application of LEFM is
under these conditions, due to the large plastic volumes formed around crack tip that
considerable influence their behaviour, usually not adequate for such structures,