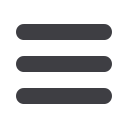
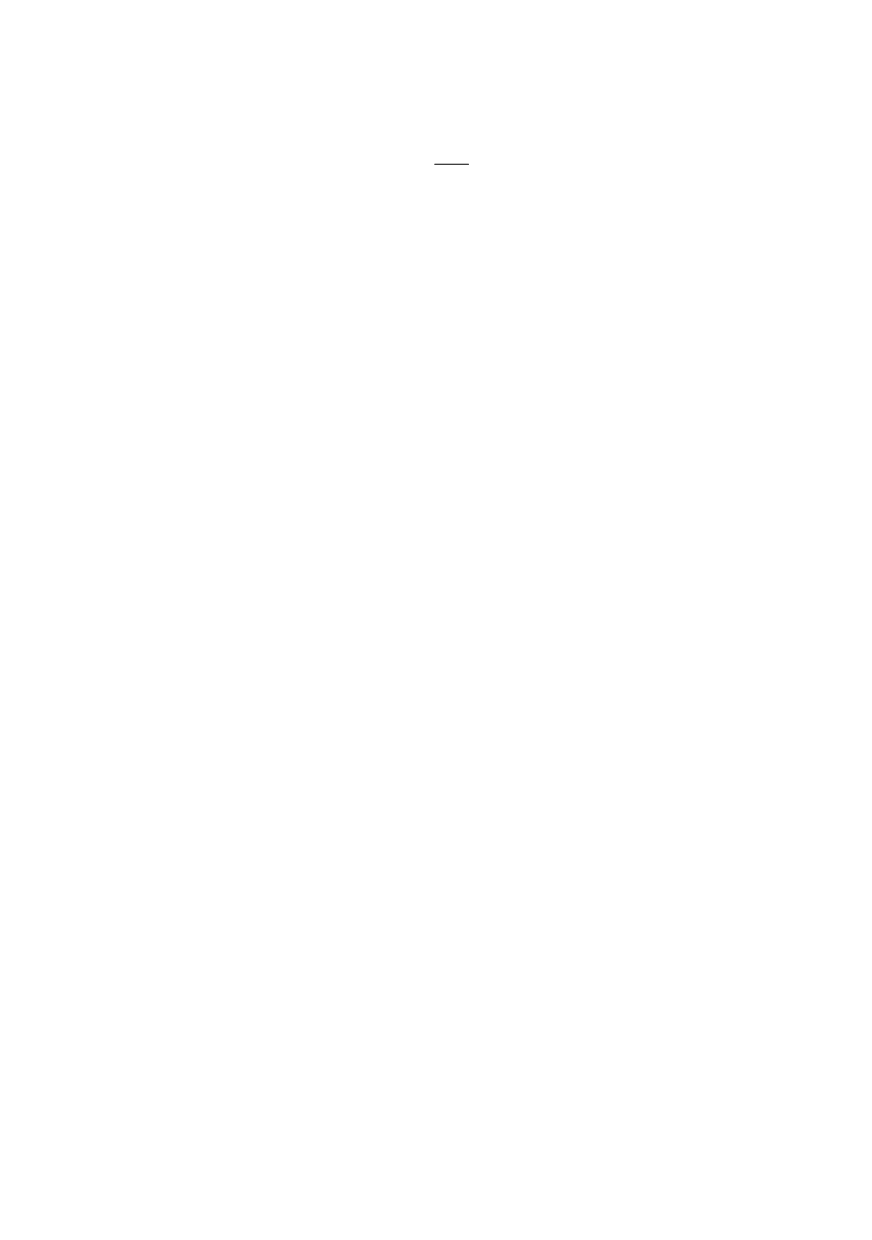
33
Based on HRR solution the same relationship can be written in slightly different form,
but so that is not limited to LEFM range
o
n
J
d
σ δ
=
(25)
where
d
n
is dimensionless
constant that depends on material characteristics
(
ε
o
,
ν
,
α
) and
stress state (plane stress or plane strain). In fact
d
n
depends strong on
n
and week on
σ
o
/
ε
.
For plane strain is
d
n
≈
0.3 – 0.65
and for plane stress:
d
n
≈
0.5 – 1.07
(max for
n
→ ∞
).
Because the structural steels of medium strength usually have
n
in the range 8 to 12, the
d
n
value for such materials under plane strain conditions is approximately 0.5.
Similar experiments (
K
Ic
, K
R
,
and
J
Ic
,
da/
Δ
N
) serve for the evaluation of material
fracture resistance, but test with CTOD have found application mainly in offshore
structures. Calculation based on CTOD is carried out in the same way as in the case of
J
-
integral. So calculated design curve is recommended (Fig. 15) in standards.
The application of this curve is appropriate for ductile fracture with large deformation.
In case of brittle materials the measurements are less accurate, and the application is
inconvenient. One of the most stimulating reasons of CTOD application is the expectation
that for heterogeneous materials, like welded joints, this can be more usable.
However, CTOD procedure in case of under matched welded structures predicts
significantly lower values for crack driving force as in reality, and for overmatching cases
the use of base metal tensile properties will produce over-conservative predictions.
Especially for the case of under matching if
ε
f
/
ε
Y
> 0.5 the application should be avoided.
3.4. Analysis of tearing instability
Until now the use of different parameters of fracture has been concentrated on crack
initiation at critical values of
J
,
K
or
CTOD
. However, the ductile materials posses the
growing resistance curve in form (
J, K, CTOD) = f(
Δ
a)
) that indicates the fracture must
not appear at initiation or when the critical values as
J
Ic
has been achieved. Depending on
the geometry and loading, slow, stable crack growth is often observed prior to fracture
instability. The analysis of crack growth up to the instability point is important for
calculation of the maximum load carrying capacity of fractured structure or component
and understanding of crack tearing is important in practice. Nevertheless, the attention
should be given to the fact that for some materials, as the aluminium alloys, the resistance
curve is almost with no increase.
Figure 16 shows that instable crack growth appears when the driving force change
rate, expressed by the slope which depends on loading and crack growth, exceeds the
increase in material resistance. However, conditions in this respect depend on the way
how a structure is loaded. When the load is fixed, the crack driving force increases with
crack extension. Because of this, the load controlled structure is more prone to the
instability. If the deformation of the structure is constant, the crack driving force falls
with the crack growth, so that the probability of stable crack growth is significantly
higher. In reality many structures are under conditions somewhere between. To make this
more clearly these two extremes are compared in Fig. 17.