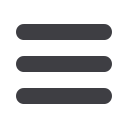
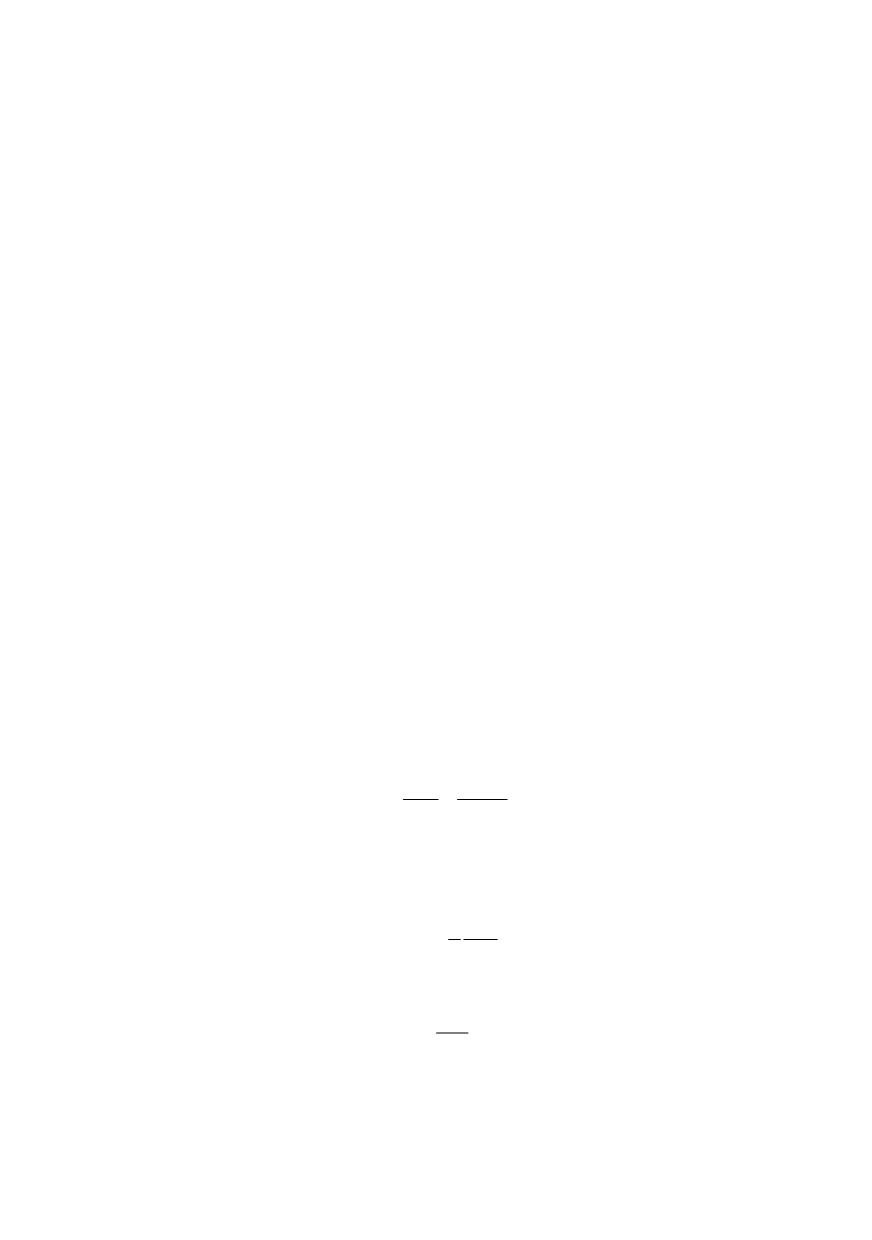
168
The simplicity of this approach is clear when, in addition to remote stress,
σ
,
the
residual stress,
σ
zn
is taken into account through the equivalent remote strain
ε
:
(
)
zn
/ E
ε
σ σ
= +
(2)
where
E
modulus of elasticity. Stress concentration factor,
k
I
, can also be included
(
)
1
I
k
/ E
ε
σ
= −
(3)
Japanese Welding Society developed standard WES 2805 to assess the integrity of
welded structures (JWES 2805 Procedure /8/), using elastic-plastic fracture mechanics
and CTOD (
δ
) concept
for estimating the significance of defects in welded joints.
Imperfection, detected by nondestructive testing, can be simplified by an ideal form,
as semi-elliptic surface or elliptic embedded crack, and then use equivalent length of
corresponding through crack based of the linear elastic fracture mechanics (LEFM).
Significance of imperfection is evaluated by the condition:
crack driving force > material crack resistance
(4).
for possible crack initiation,
crack driving force < material crack resistance
(4a)
when crack effect might be neglected.
Crack driving force is determined by fracture mechanics formulae, and material crack
resistance by CTOD standard testing /6/. Remote strain,
ε
, is determined by summing up
the primary strain
ε
1
(due to applied load), secondary strain
ε
2
(due to residual stress and
geometry irregularities) and secondary strain
ε
3
(
due to stress concentration)
.
Engineering treatment model (ETM)
This is EFAM ETM 97 procedure /9/, using expressions for determining CTOD based
on elastic-plastic fracture mechanics (EPFM). This procedure was developed in GKSS,
Geesthacht, Germany in 1997 and represents a part of methodology on determining the
significance of imperfections, such as cracks, in welded joints.
In elastic range, when the load,
F
, is lower than net section yielding load,
F
Y
,
F
<
F
Y
,
crack tip opening, defined as
δ
5
,
is presented as:
2
1
5
2
ef
Y
K K
E mE
β
δ
δ
= +
(5)
where
β
= 2.41 √mm and
m
= 1 for plane stress condition, or,
β
= 2.09 √mm and
m
= 2
for
plane strain condition, and
K
ef
is effective stress intensity factor corresponding to effective
crack length,
a
ef
, defined as:
2
2
1
2
ef
ef
Y
K
a a
πδ
= +
(6)
Alternatively,
J
integral can be applied, introduced by the relation:
2
ef
K
J
E
=
(7)
where
δ
5
can be defined through
J
-integral combining Eq. (7) and Eq. (5)
An important feature of ETM procedure is possible application to heterogeneous
materials, that is, to welded joints with mismatch effect greater that 10%.