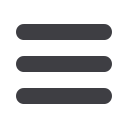
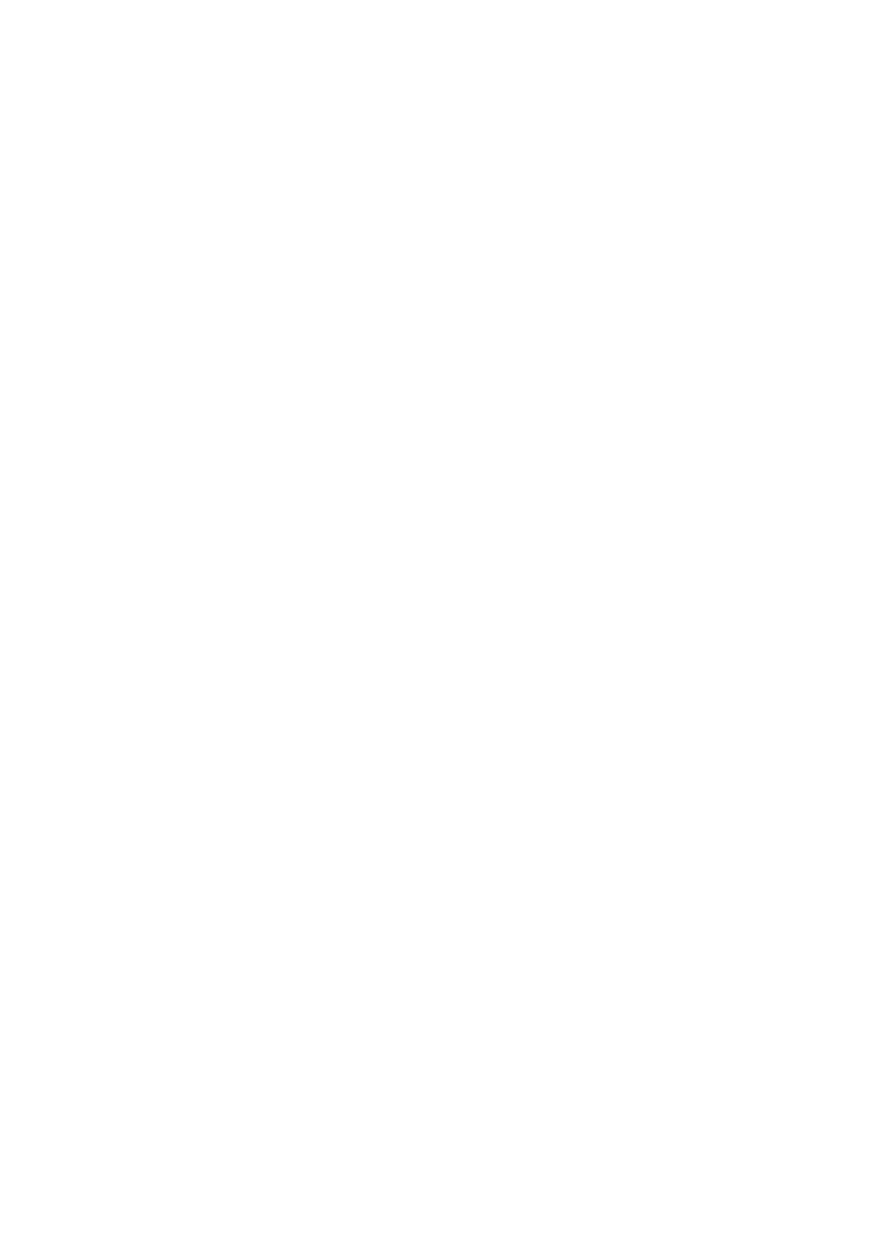
344
Structural integrity assessment is based on inevitable simplifications. In that sense the
problem can be considered as a specific approach to structural reliability. Basic
presumption is the homogeneous microstructure, acceptable in some cases at macro and
eventually at micro level, but it can not be applicable with a certainty at nano level. This
assumption is far for being real even at macro level, i.e. for welded structures.
The way past to understand the fracture of structural compnents and its mechanisms is
relatively long /3/. In the beginning of systematic analysis the knowledge about this
matter was very limited and the problem is considered by gathering new experience and
developing new theories, experimental and numerical procedures. But a lot has to be
done more entering to nano level.
It is not an easy task to make the conclusion about this fast developing matter.
Instead, some considerations from Ref. /26/ are quoted. “At the macro scale, the point at
which a material will fail or break depends on its ability to maintain its shape when
stressed. The atoms of ductile substances can shuffle around and remain cohesive longer
than brittle, which contain structural flaws acting as failure points. At the nano scale,
these structural flaws do not exist. These objects are so small that most of the atoms
reside on the surface. According to Namboodiri and Kim, the properties of more mobile
surface atoms, not bounded on all sides, dominate at the nano scale. This dominance gi-
ves an otherwise brittle material (silica) its counterintuitive fracture properties”
.
The story about fracture, crack and crack tip is more and more far from its end by
gathering more knowledge and applying more sophisticated approaches thanks to
experimental and numerical methods, such as atomic force microscope and powerful
computers and softwares. Considering crack surfaces as a typical kind of interface, it is
necessary to find out actual limits that can help to understand fracturing process at dif-
ferent scales. Provisional and temporary conclusion about considered matter is explained
probably in the best way in Ref. /27/ in a way:” We can distinguish between interfaces in
general and nano-interfaces as follows: Typically, an interface separates two bulk phases;
we define, consistent with the above definition, a nano-interface as one in which the
extent of one or more of the phases being separated by the interfaces is nanoscopic. In
nanointerfaces we include nano-interconnects, which join two or more structures at the
nanoscale. For nanointerfaces, traditional surface science is generally not applicable.”
It is clear from ship fracture case study that some material property might be not
discovered and that actual problem could be solved only if this property was recognised,
characterised and specified for given circumstances. This could be more pronounced in
the case of fatigue (e.g. for low cycle fatigue) or in the case of creep. Having in mind the
development stage of nano structure, one can expect more uncertainties in the case of
nano materials, suggested in performed research of the ductile behaviour found at nano
level for material brittle at macro level /26/.
Stress, defined as the ratio of load and the size of loaded area, is the fundamental
value in engineering calculations. So defined, stress became most used value in struc-
tures for analysis and comparison with characterized material strength properties.
However, the area is of final size at macro level under accepted assumptions, and this is
not the case at nano level. Using the fracture atomic model (Fig. 6), stress at nano level
could be considered as the sum of atomic forces rather than through area, difficult to be
defined in model with distinct atoms arrangement.
The defects, including crack, can not be considered in the same way in macro and in
nano structures. It is not possible to interpret crack tip and its severity in nano material,