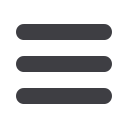

146
Mechanically induced residual stresses are caused by non-uniform permanent defor-
mation when a metal is mechanically stretched or compressed under restraint. The occur-
rence of mechanically induced residual stresses requires the presence of both. Permanent
mechanical deformation and restraint, that prevents the deformed metal from contracting
or expanding to its new unrestrained equilibrium dimension. In general, the sign (tension
or compression) of mechanically induced residual stress is opposite to the sign of non-
uniform plastic strain that produced the residual stress. This process is used to mechani-
cally curve or straighten components and, as in peening, which produce a compressive
stress layer on the component surface to improve its fatigue or corrosion behaviour.
Fabrication by welding usually results in stresses that are locked into the fabricated
assembly. These stresses are either residual stresses or reaction stresses, or both. Residual
stresses are caused by the inability of the deposited molten weld metal to shrink freely as
it cools and solidifies. Reaction stresses are caused by the inability of assembly compo-
nents to move relative to each other during thermal expansion and contraction of the de-
posited weld metal, or the molten base metal for autogenously welded joints and sur-
rounding base metal. Contraction of solidifying weld metal is restricted by adjacent mate-
rials, resulting in three-dimensional residual stresses. The magnitude of these stresses
depends on several factors, like size of the deposited weld bead, weld sequence, total
volume of the deposited weld metal, weld geometry, and strength of the deposited weld
metal and of the adjoining base metal. Often, the magnitude of these stresses exceeds the
elastic limit of the lowest strength region in the weldment.
Methods for measuring residual stresses are sectioning, drilling hole, and X-ray diffra-
ction. The sectioning method is a destructive test in which residual stresses are determi-
ned by removing slices from the member and measuring the resulting strain. Drilling hole
is a semi-destructive test for measuring residual stresses near the material surface; it invo-
lves placing strain gauges on the surface and measuring strain relaxation by drilling hole
in the vicinity of the gauges. The X-ray diffraction method is a non-destructive test in
which surface residual stresses are determined by measuring the change in the lattice spa-
cing of the material; only surface residual stresses are measured in a localized area.
Development of residual stresses in a groove welded joint is shown in Fig. 1 /1/.
Figure 1: Residual stresses for a butt-welded plate /1/
As the deposited molten metal cools, it contracts longitudinally along and transversely
across the weld, Fig. 1. Surrounding base metal prevents the contraction, producing resi-
dual tensile (+) and compressive (-) stresses. These stresses may cause distortion,