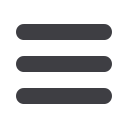
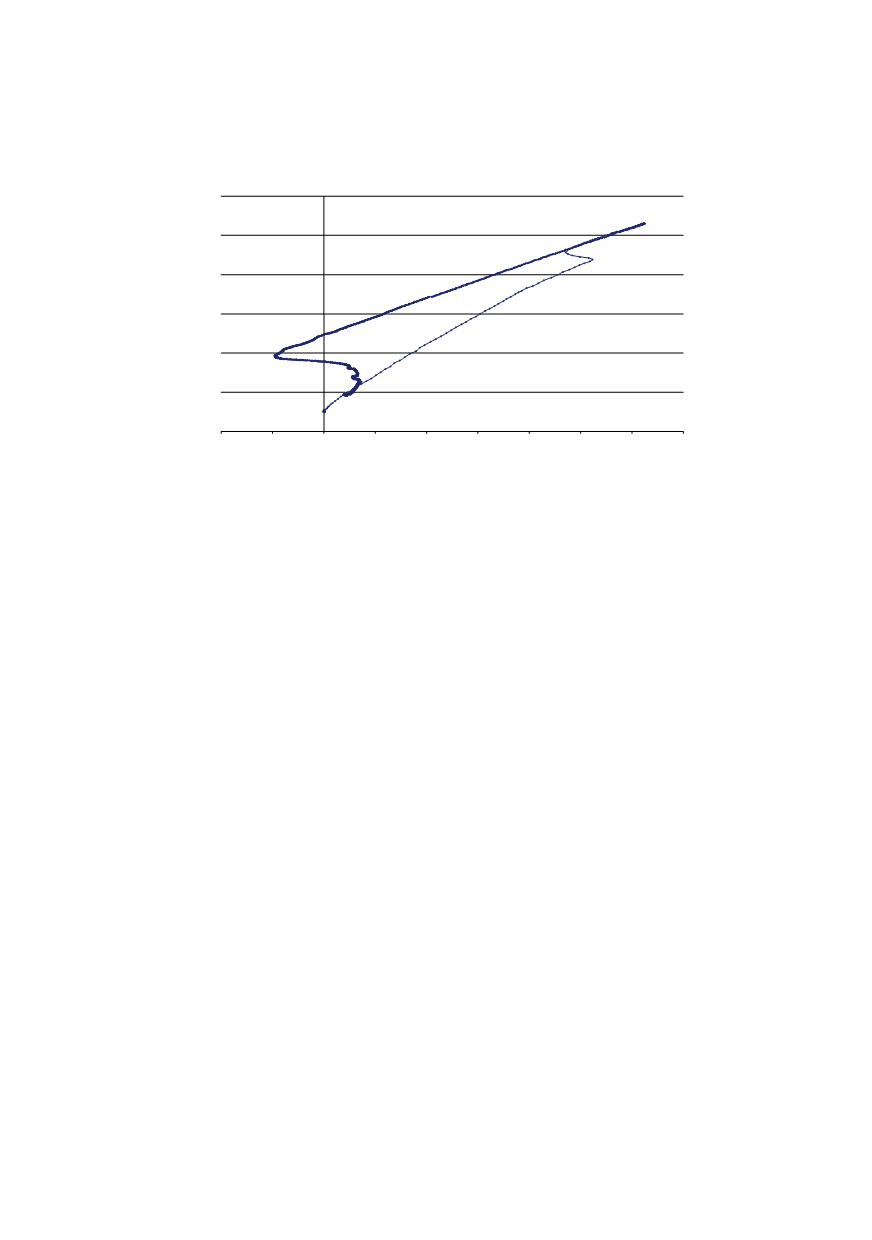
305
500°C, t
8/5
, 40 sec. After welding, the samples were subjected to PWHT at 730°C for 1
hour. Then all samples were subjected to inspection of microstructure and measurement
of hardness.
Figure 7: Dilatometric curve
6.2. Material
The appearance of microstructures at temperatures of 925°C, 1100°C, 1300°C and
1386°C is shown in Fig. 8. The microstructure corresponding to austenitisation
temperature of 925°C, Fig. 8 a, consists of martensite with less prominent martensite
laths. At some previous austenitic grain boundaries, the presence of coarser carbides
above 1 µm was observed. The presence of the carbides is most probably the result of
keeping at austenitisation temperature for a short time, considering that the carbides of
M
23
C
6
type completely dissolve at temperatures above 900°C /19/.
The microstructure corresponding to austenitisation temperature of 1100°C, Fig. 8 b,
consists of tempered martensite with clearly visible martensite laths. Coarser carbide
particles above 1µm are still present.
The microstructure corresponding to austenitisation temperature of 1300°C, Fig. 8 c
and 1386°C, Fig. 8 d, also represents tempered lath martensite. Carbide particles above
1µm at the boundaries of previously austenitic grains practically are not present.
6.3. Hardness
Hardness of parent metal of 230 HV1 was measured. Variation of hardness of
simulated samples with temperature of simulation showed a drop at 925°C, Fig. 9, and
that is why this temperature of 925°C was chosen as representative of “soft zone”.
A significant drop of hardness of almost 40HV occurs at simulation temperature of
850°C that is somewhat above A
C1
temperature. With an increase of simulation
temperature, ferrite fraction transforming into austenite increases. At temperature of
925°C, this fraction was approx. 90%. At this temperature, there was no considerable
dissolution of carbides and nitrides and transformation of C and N into solid austenite
solution. Therefore, martensite formed at cooling had significantly lower content of C and
N. Due to decreased content of C and N, repeated separation of M
23
C
6
carbides and MX
carbonitrides during subsequent heat treatment was limited resulting in hardness lower
than that of base metal.
Dilatometric curve at 1050°C
0
200
400
600
800
1000
1200
-40
-20
0
20
40
60
80
100
120
140
Dilatation [μm]
Tp [°C]