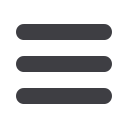
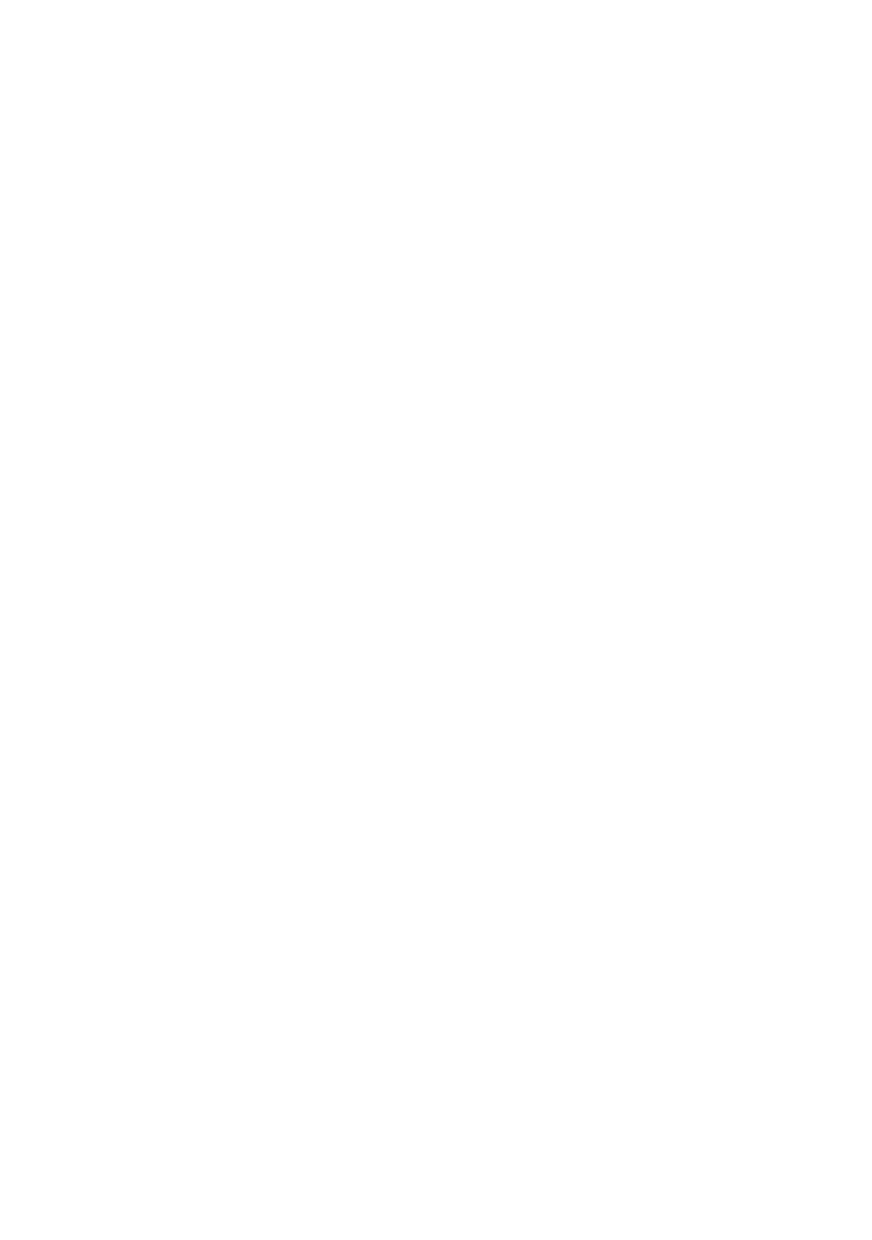
194
platesEN 10160 quality class S2 – E3, and for castings EN 12680–1 severity level 3.
Testing techniques and scopecan be specified based on product quality and acceptance
level.
2.5. Testing procedure specified in written form
ASME, Sec. V and majority of European Standards (EN 12062: 2002 ′′Common rules
for non-destructive testing of metallic materials′′) request to present written procedure –
specified instruction for tested subject inspection by selected testing method. Instruction
should define testing techniques and parameters.
Program for the instruction composition for welded joints testing by x-ray, which
includes all the limitations, is available in EN 1435: 2003.
It might be requested to deliver the instruction for verification or to be presented to the
purchaser representative or authorised inspector.
2.6. Verification of testing parameters
Testing parameters have to be verified during procedure and proof the testing quality
before the decision of tested subject is made. For example:
• In ultrasonic testing, in addition to parameters cited in a part ′′Calibration of the
equipment′′ every four hours must be controlled distance range and sensitivity settings,
and in case of excessivedeviation all tests performed after last control must be repeated.
• In the magnetic particles inspection should be controlled: particles concentration in
the suspension,suspension susceptibility(using control block No. 1 or No. 2),-tangential
magnetic field capacity and/or magnetisation amperage,illumination of testing surface or
UV radiation and testing surface back illumination.
•In the x-ray testing it is to control: the level of backside radiation (lead number ′′B′′
on the cassette back side), film chemical procedure (using in advance exposed band), the
existence of requested marks on the radiograph,the existence of artefacts in considered
zones, radiograph darkness, and image quality value, and if some of these parameters
deviates of allowed value, the radiograph can’t be used for evaluation of tested subject.
2.7. Testing performance
Different testing levels might be applied according to required quality level of pro-
duct. For example, when testing welded joints:
• In x-ray tests two levels are defined, class A – base techniques, and class B –
advanced techniques. These classes differ in the value of minimal distance between
source and film, quality of used film and requested image quality value.
• In the ultrasonic tests four testing levels (A, B, C and D) are specified. The increased
probability of detection from level A to level C is achieved by increased covering that is
by scanning number (more scanning directions, more angles propagation, and surface
flattening). Testing level D is aimed for special applications.
2.8. Personnel in non-destructive testing
The greatest contribution in non-destructive testing is achieved by the request that
only personnelqualified and certified by corresponding standard can perform the testing.
In Europe it is EN 473: 2000 ′′Qualification and certification of NDT personnel′′
(harmonized standard of EC 23/97 directive).
Personnel in NDT are classified at three levels: