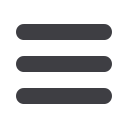
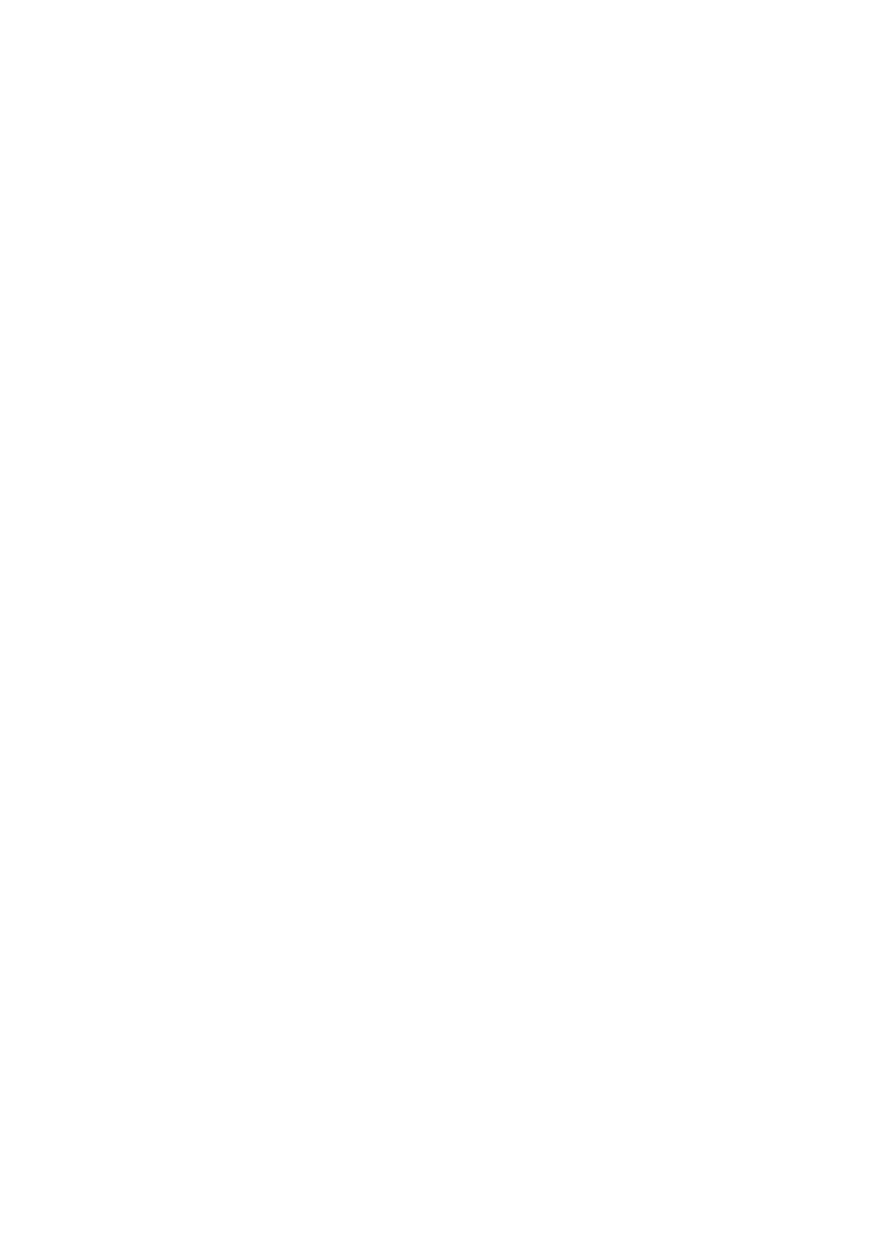
191
APPLICATION OF NON-DESTRUCTIVE TESTING PROCEDURES FOR
STRUCTURAL INTEGRITY ASSESSMENT
Stevan Kuzmanović
Energoinvest-IMQ, Sarajevo, Bosnia and Herzegovina
s.kuzmanovic@lsinter.netAbdulah Koro, Nedžib Njuhović
Energoinvest-IMQ, Sarajevo, Bosnia and Herzegovina
1. INTRODUCTION
Non-destructive testing methods are used for detection of discontinuities, defects and
imperfections in products, primarily in casings, forgings, plates, pipes, and weldments.
In general, these deficiencies can be divided in that developed:
1.
in casting process of row material;
2.
during manufacturing by rolling, forging, cutting, welding;
3.
in exploitation of components and equipments.
Detrimental effects can be avoided or significantly reduced if deficiencies are detected
in an early stage of manufacturing or service. For that, the role of non-destructive testing
(NDT) is of high importance for structural integrity and life of equipment in service.
Basic knowledge about NDT methods and procedures can be found in textboxes and
literatures, including many lectures held in the previous International Fracture Mechanics
Summer Schools (IFMASS). With this in mind, in addition to classification of imper-
fections and defects, state-of-the-art in the improvement of NDT performance in practice
will be presented here, followed by the examples of recent NDT applications.
2. IMPERFECTIONS AND DEFECTS
Most important deficiencies in equipment and their components are imperfections and
defects. Short overview of them can help to follow next text in an easier way.
2.1. Classification of imperfections
In general, imperfections are classified depending on manufacturing process, type of
material, thickness and other
factors.So, in steel castings to 50 mm thick, discontinuities
detectable by radiography are grouped in ASTM E446 standard as follows:
•A – gas porosity,
• B – inclusions of slag and sand,
• C – shrinkage cavity,
• D – cold crack,
• E – hot crack,
• F – inserts,
• G – marble air.
Geometrical imperfections in metallic materials, formed in arc melting process, are
classified in EN ISO 6520-1 as follows:
• 100 – cracks,
• 200 – voids,
• 300 – inclusions of solids,